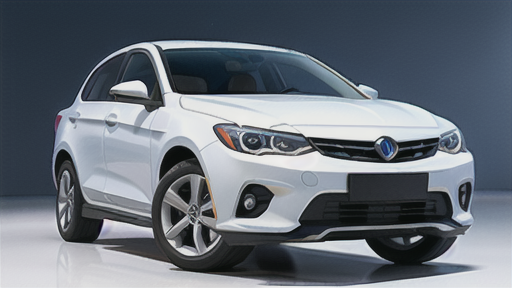
車の製造とロット管理の重要性
製造業では、製品を作る際にまとめて同じ作り方で、同じ材料を使って連続して生産します。このまとまりの単位のことをロットと言います。自動車作りでは、小さな部品から完成した車まで、色々な段階でこのロットという考え方が使われています。部品を作る時、同じ型を使って作られた部品たちは一つのロットとして扱われます。例えば、車のドアを作る型があって、その型を使って100個のドアを作ったら、その100個のドアは同じロットになります。他にも、同じ色で塗装された車体も同じロットとしてまとめられます。
このロットという考え方を使った管理をロット管理と言います。ロット管理は、製品の品質を保ち、製品がどこで作られ、どのような過程を経てきたのかを追跡できるようにするために、とても大切な役割を果たします。もし、あるロットの製品に欠陥が見つかったとします。そうすると、同じロットで作られた他の製品にも同じ欠陥があるかもしれないと予測できます。だからロット管理をしていれば、問題のある製品をすぐに見つけて回収したり、対策を考えたりすることができるのです。
また、それぞれのロットにはロット番号が付けられています。この番号を管理することで、その製品がいつ、どこで、どのように作られたのかという履歴を調べることができます。これは、もし何か問題が起きた時に、その原因を調べたり、同じ問題が起きないように対策を立てたりするのにとても役立ちます。自動車はたくさんの部品が組み合わさってできています。一つの部品に問題があると、それが他の部分に影響を与え、大きな問題に発展することもあります。だから、自動車作りでは、特にロット管理が重要になります。どの部品が、いつ、どこで作られたのかをきちんと管理することで、品質の高い車を作ることができるのです。