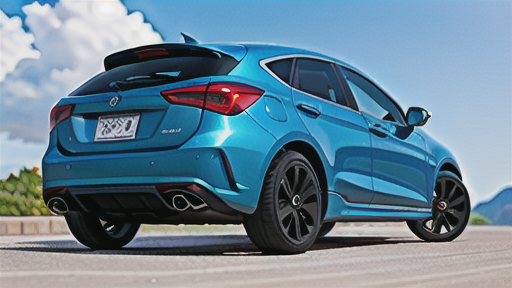
金型部品:バックプレートの役割
抜き型、特に厚手の板材を打ち抜く際に用いられる型部品の一つ、それが「控え板」です。控え板の役割を理解するには、まず抜き型の仕組みを知る必要があります。抜き型は、上下に配置された二つの部品で構成されています。上の部品をポンチ、下の部品をダイと呼び、このポンチとダイの間で材料を挟み込み、ポンチをダイに押し込むことで目的の形に材料を打ち抜きます。
厚い板材を打ち抜く作業では、ポンチに非常に大きな力がかかります。この大きな力は、ポンチの摩耗や破損を招き、型全体の寿命を縮めてしまう原因となります。そこで活躍するのが控え板です。控え板はポンチの裏側に配置され、ポンチに加わる力を分散し、負担を軽減する役割を担います。ちょうど、人間の体に鎧を装着するように、ポンチを支え、保護する役割を果たすのです。
もし控え板がない場合、ポンチは過大な力に耐えきれず、すぐに摩耗したり、最悪の場合は破損してしまうこともあります。これは、生産効率の低下や、修理費用など、様々なコスト増につながる可能性があります。
適切な控え板を使用することで、ポンチにかかる負担を軽減し、ポンチの寿命を延ばすことができます。さらに、型全体の寿命も延び、安定した製品生産にも繋がります。材料の厚さや抜き加工の形状に応じて、適切な材質・形状・大きさの控え板を選ぶことが、高品質な製品を安定して生産するための重要な要素となります。控え板は、いわば縁の下の力持ちであり、抜き型の安定稼働に欠かせない重要な部品と言えるでしょう。