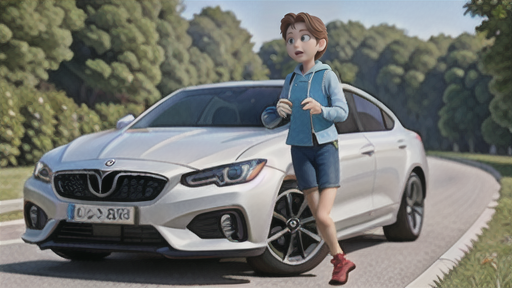
試作ラインの重要性
試作行程とは、新しい車を造る上で欠かせない、いわば舞台の本番前に設けられた予行演習の場です。完成車製造行程を本格的に稼働させる前に、小規模で試験的に車を作り、様々な検証を行うための特別な工程のことを指します。これは、新しい料理の作り方を思いついた際に、実際に作って味を確かめる作業に似ています。どんなに素晴らしいレシピを考案したとしても、実際に調理して口にしてみなければ、本当に美味しいのか、改善すべき点はないのかは分かりません。車作りにおいても全く同じことが言えます。設計図の上では完璧に見えても、実際に部品を組み合わせて形にしてみなければ、隠れた問題点や改善の余地は見つかりません。
試作行程では、少量の車を実際に組み立てながら、新しい製造方法や導入した機械の性能、作業の効率などを細かく調べます。具体的には、新しい部品が設計通りに機能するのか、組み立て工程に無理がないか、作業者は安全に作業できるか、想定した通りの時間で組み立てられるかなどを確認します。また、実際に組み立てられた試作車を走行させて、走行性能や安全性、快適性なども評価します。これらの検証を通して得られた知見は、設計や製造工程の改善に役立てられます。
試作行程で入念な確認と調整を行うことで、完成車製造行程における大きな問題発生を未然に防ぎ、円滑な稼働開始を実現できるのです。いわば、本番の舞台の前に設けられたリハーサル会場のようなもので、ここで念入りなチェックと調整を行うことで、完成車製造行程での成功、ひいては高品質な車の生産へと繋がります。試作行程は、高品質な車を生み出すための重要な土台と言えるでしょう。