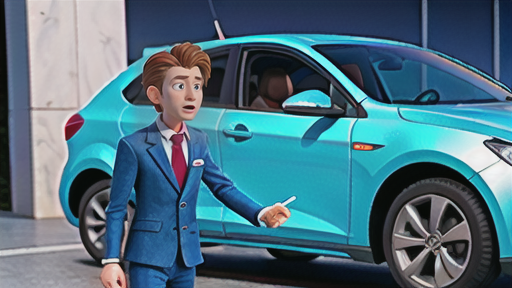
静電気の発生と対策
物はすべて、目には見えないほど小さな粒が集まってできています。この小さな粒は原子と呼ばれ、さらに原子の中心にはプラスの電気を持つ原子核と、その周りをマイナスの電気を持つ電子が回っています。通常はプラスとマイナスの電気が同じ量だけあるので、全体としては電気的に中性で、電気が流れたり体に感じたりすることはありません。しかし、例えば乾燥した寒い日にセーターを脱ぐと、セーターと体がこすれ合います。すると、セーターにあったマイナスの電気が体に移動し、体にはマイナスの電気が多くなり、セーターには少なくなります。この状態を静電気と言います。静電気とは、電気が動かず、物体に留まっている状態のことを指します。まるでダムに水が溜まっているように、体にマイナスの電気が溜まっているのです。
この溜まった電気が、金属のドアノブなど電気が流れやすい物に触れると、一気に流れ出します。この現象が放電です。放電する際に、パチッという音や光、軽い衝撃を感じることがあります。これが冬場にドアノブに触れた時などに experience する静電気の正体です。静電気は、日常生活でよく起こる現象で、大抵の場合は体に害はありません。しかし、溜まった静電気が大きい場合、火花が発生し、可燃性のガスなどに引火して火災を引き起こす危険性もあります。また、精密な電子機器に静電気が流れ込むと、故障の原因となることもあります。静電気は、乾燥した環境で発生しやすいため、加湿器などで湿度を上げたり、帯電防止グッズを使用するなど、静電気を抑える対策も大切です。