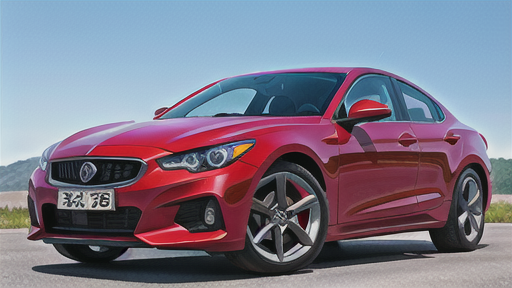
クルマづくりを支える技術規格
車は、数多くの部品が組み合わさって作られています。まるで巨大なパズルのように、一つ一つの部品が正確に組み合わさることで、初めて安全に走ることができるのです。このパズルのピースを正しく作るための設計図となるのが、技術規格です。
技術規格とは、車の設計や製造、検査など、あらゆる工程において、基準となるものです。大きさや材料、性能など、様々な項目が細かく決められています。例えば、ネジ一つとっても、その太さや長さ、素材などが厳密に定められています。これは、どの工場で作られたネジでも、同じように使えるようにするためです。このように、技術規格は、部品の互換性を保証する上で重要な役割を果たしています。
また、技術規格は、車の安全性を高める上でも欠かせません。ブレーキの性能やシートベルトの強度など、安全に関連する部品には、特に厳しい規格が適用されています。これらの規格を満たすことで、万が一の事故の際にも、乗員の安全を守ることができるのです。
さらに、技術規格は、車の品質を維持するためにも必要です。すべての部品が規格通りに作られているかを検査することで、不良品の出荷を防ぎ、高い品質を保つことができるのです。
技術規格は、常に更新されています。新しい技術が開発されたり、より高い安全性が求められるようになったりすると、それに合わせて規格も見直されます。このように、技術規格は、車の進化と共に変化し続けているのです。まるで生き物のように、常に成長を続ける車の技術を支える、重要な役割を担っていると言えるでしょう。