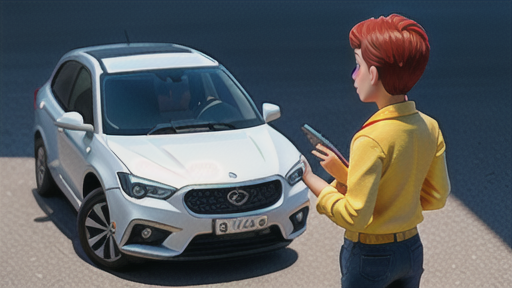
車の製造におけるガスシールドアーク溶接
自動車を作る上で、金属部品同士を繋ぎ合わせる溶接は欠かせません。車体はたくさんの金属部品を組み合わせて作られており、これらをしっかりと固定するために溶接が用いられています。溶接の良し悪しは、自動車の安全性、長持ちするか、そして見た目にも直接関わってきます。そのため、自動車を作る会社は常に質の高い溶接を行うための技術開発に力を入れています。
近頃は、車体を軽くすると同時に強度を高めることが求められており、溶接技術の重要性はさらに高まっています。溶接にも様々な種類があり、目的に合わせて最適な方法が選ばれます。例えば、点溶接は、薄い鋼板を接合する際に用いられる代表的な方法です。電極で鋼板を挟み込み、電流を流すことで金属を溶かして接合します。この方法は、溶接時間が短く、効率的に作業を進められるため、大量生産される自動車の製造に適しています。
また、アーク溶接は、金属にアークと呼ばれる電気の火花を発生させて溶接する方法です。この方法は、点溶接に比べて強度の高い接合が可能であり、厚い鋼板の溶接にも適しています。さらに、近年ではレーザー溶接も注目を集めています。レーザー光線を用いて金属を溶かすレーザー溶接は、非常に精密な溶接が可能です。そのため、高い精度が求められる部品の接合に用いられています。
このように、自動車の製造において溶接は非常に重要な役割を担っており、様々な種類の溶接方法が使い分けられています。そして、安全性や耐久性、製造効率などを考慮し、常に新しい溶接技術の開発が進められています。今後も、自動車の進化と共に溶接技術も進化していくことでしょう。