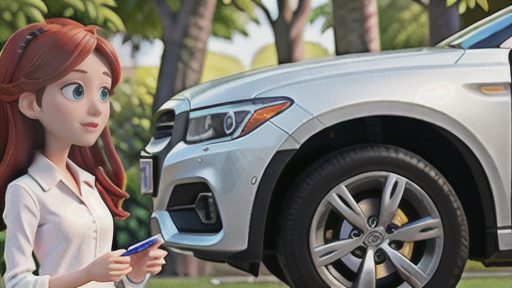
塗料の寿命:ポットライフを理解する
車体を彩ったり、傷を直したりする際に活躍するのが、二液型の塗料です。この塗料は、主剤と硬化剤を混ぜ合わせて使用します。混ぜ合わせることで化学反応が始まり、塗料が硬化していきます。この化学反応の開始から、実際に塗装作業ができるまでの限られた時間を「ポットライフ」と呼びます。つまり、混ぜ合わせた塗料が使える時間のことです。
ポットライフは、塗料の種類によって大きく左右されます。例えば、速乾性の塗料はポットライフが短く、ゆっくり乾く塗料はポットライフが長くなります。また、気温や湿度などの周りの環境もポットライフに影響を与えます。気温が高いほど化学反応が速く進むため、ポットライフは短くなります。反対に、気温が低い場合はポットライフは長くなります。湿度も同様に、高い場合はポットライフが短くなる傾向があります。
ポットライフを正しく理解することは、美しい仕上がりを得る上で非常に大切です。ポットライフを過ぎた塗料を使用すると、粘度が高くなり、均一に塗ることが難しくなります。また、硬化不良を起こし、表面がデコボコになったり、ひび割れが生じたりする可能性があります。このような仕上がりになってしまうと、再塗装が必要になることもあり、時間と手間がかかってしまいます。さらに、ポットライフを把握することで、塗料を無駄にすることも防げます。必要な量だけを混ぜ合わせることで、使い切れずに固まってしまう塗料を減らすことができます。
美しい仕上がりを実現し、塗料を無駄にしないためにも、作業前に塗料のポットライフを確認し、気温や湿度に注意しながら、時間内に使い切るように心がけましょう。また、一度に大量に混ぜるのではなく、数回に分けて混ぜることで、ポットライフを有効に活用できます。適切な量の塗料を混ぜ、時間内に使い切ることで、無駄なく、美しく仕上げることができます。