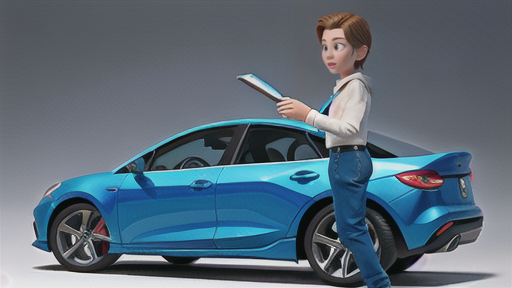
車の心臓部、軸受の秘密
車はたくさんの部品が組み合わさって動いています。その中で、回転する部品同士の摩擦を減らし、滑らかに動かすという大切な役割を担っているのが軸受です。くるまが円滑に動くために、軸受はなくてはならない部品です。
軸受は、エンジンやタイヤなど、車の様々な場所に使用されています。それぞれの場所で使用される軸受は、求められる性能や大きさ、用途によって様々な種類があります。例えば、エンジン内部のように高温になる場所では、熱に強い特別な軸受が使われています。高温に耐えられる材料で作られた軸受は、エンジンの正常な動作を支えています。また、高速で回転する部分では、摩擦によるエネルギーのロスを極めて少なくするために、精密に作られた軸受が用いられています。
軸受には大きく分けて、ころがり軸受とすべり軸受の二種類があります。ころがり軸受は、軸と軸受の間に小さな玉やローラーを挟むことで、摩擦を少なくし回転を滑らかにしています。自転車や扇風機など、身近な製品にも使われています。一方、すべり軸受は、軸と軸受の間に油やグリースなどの潤滑剤を入れることで、摩擦を減らして滑らかに回転するようにしています。時計や精密機器など、より小さな摩擦抵抗が求められる場所に使用されています。
これらの軸受が正しく働くことで、車は円滑に走り、燃費も良くなります。軸受の性能が車の燃費や走行性能に直結するため、軸受の開発は常に進歩を続けています。より摩擦の少ない軸受や、より耐久性の高い軸受が開発されることで、車はさらに進化していくでしょう。