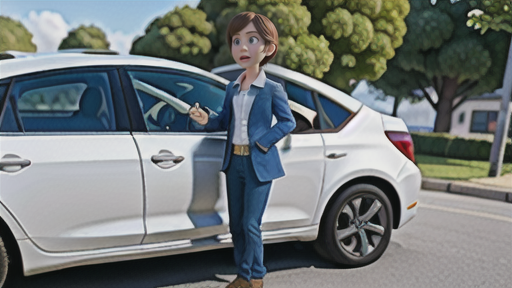
車の錆を防ぐウオッシュコート
洗い塗りとは、金属の表面を保護し、錆の発生を抑える塗装方法です。名前の通り、金属表面を薄く覆うように塗料を塗布し、まるで薄い膜で包み込むかのようです。この膜が、錆の原因となる水や空気中の酸素が金属に触れるのを防ぎ、腐食から守ります。
洗い塗りに使う塗料は、密着性と防錆力に優れた特別な塗料です。よく「洗い下地塗料」や「腐食止め塗料」と呼ばれています。これらの塗料は、金属表面にしっかりとくっつき、剥がれにくいため、長期間にわたって金属を保護することができます。
洗い塗りは、車の車体だけでなく、様々な金属製品に使われています。例えば、橋や建物などの大きな構造物、自転車や家電製品などの日用品、さらには工場で使われる機械など、様々な場面で金属の腐食を防ぎ、製品の寿命を延ばすために役立っています。
洗い塗りの効果を高めるためには、塗る前の下地処理が重要です。金属表面の汚れや油分をしっかりと取り除き、清潔な状態にしてから塗料を塗布することで、塗料がしっかりと密着し、より効果的に錆を防ぐことができます。また、塗料の種類や塗り方によって、耐久性や仕上がりが変わるため、用途に合った適切な塗料を選び、正しい方法で塗布することが大切です。
このように、洗い塗りは、金属製品を守る上で欠かせない技術であり、私たちの生活を支える様々な製品の耐久性を高める重要な役割を担っていると言えるでしょう。