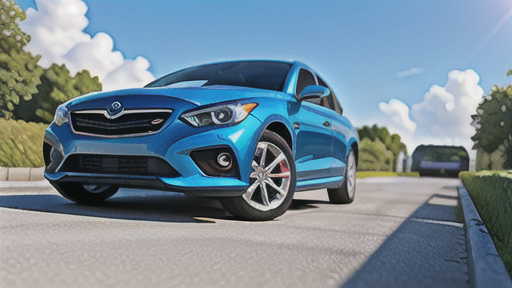
コストペナルティ:車産業発展の壁
車は、私たちの暮らしを支えるなくてはならない乗り物です。通勤や通学、買い物、旅行など、様々な場面で利用され、人々の移動の自由を支えています。特に地方では、車が生活に欠かせない存在となっています。
自動車産業は、国の経済を大きく動かす重要な産業の一つです。多くの部品メーカーや販売店などが関わり、数多くの雇用を生み出しています。特に、経済が発展途上にある国では、自動車産業の成長は経済全体を押し上げる力となります。人々に仕事を提供するだけでなく、技術の向上や道路などのインフラ整備も進みます。
しかし、自動車産業が発展していく過程では、様々な壁にぶつかることもあります。その一つが『製造コストの増加』です。これは、部品の価格上昇や人件費の上昇、新しい技術を導入するための費用など、様々な要因が重なって起こります。コストが上がると、車の販売価格も上がり、消費者が車を買いにくくなる可能性があります。また、企業の利益も減り、新しい技術の開発や設備投資に回せるお金が少なくなるため、自動車産業全体の成長を妨げることにもつながります。
コスト増加を抑えるためには、様々な工夫が必要です。例えば、部品の共通化を進めて大量生産したり、生産工程を効率化したり、新しい技術を導入して自動化を進めるなど、企業は様々な対策を講じています。また、国も、補助金を出したり、税金を安くしたりすることで、企業を支援しています。
このように、自動車産業は経済にとって重要な役割を果たしていますが、コスト増加という課題も抱えています。この課題を解決するために、企業や国が協力して、様々な対策に取り組んでいく必要があるでしょう。