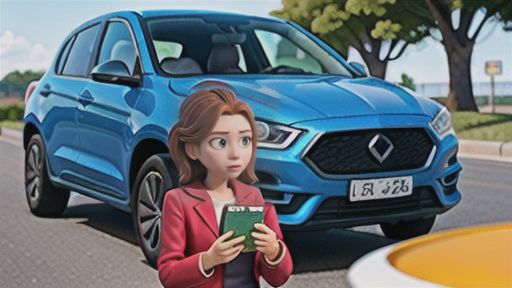
両面溶接で強度を高める
両面溶接とは、接合する材料の表側と裏側の両方から溶接を行う方法です。名前の通り、二枚の板を繋げる場合、板の両面から溶接を実施します。片面からだけ溶接する片面溶接とは異なる手法です。
溶接は、金属を熱で溶かして一体化させる技術です。溶接部分は、構造物の強度に大きく影響するため、溶接方法の選び方は、完成品の品質や安全性を左右する重要な要素となります。
両面溶接は、片面溶接に比べて、溶接部の強度を高めることができる点が大きな利点です。片面溶接の場合、溶接の開始と終了時に、クレーターと呼ばれる窪みができます。このクレーターは、強度が低く、ひび割れの起点となる可能性があります。両面溶接では、反対側からの溶接によってクレーターを埋められるため、強度不足やひび割れの発生を抑えることができます。また、両面溶接は、溶接による歪みを軽減できる効果もあります。片面溶接では、溶接時に発生する熱によって材料が変形し、歪みが生じることがあります。両面溶接では、両側から均等に熱を加えることで、歪みの発生を抑制し、精度の高い接合を実現できます。
このような利点から、両面溶接は、橋梁、建築物、船舶、自動車など、高い強度と信頼性が求められる様々な構造物の製造に広く用いられています。特に、大きな力が加わる部分や、振動、衝撃を受ける部分の溶接には、両面溶接が適しています。
ただし、両面溶接を行うためには、両側から材料にアクセスできる必要があるため、作業環境によっては適用が難しい場合もあります。そのような場合には、片面溶接で対応したり、特別な治具を用いて両面溶接を行うなどの工夫が必要となります。