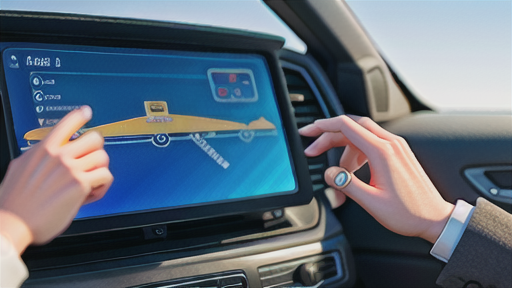
車体構造の要:コーチジョイント
車は、一枚の大きな鉄板から作ることはできません。様々な大きさや形の鉄板を組み合わせて作られています。まるでパズルのように、複雑な形を作るために、鉄板同士を繋ぎ合わせる技術が重要になります。
鉄板の組み合わせには、「コーチジョイント」と呼ばれる方法がよく使われます。これは、二枚の鉄板を特定の角度で重ね合わせ、特殊な工具を使って繋ぎ合わせる技術です。例えるなら、紙を折って組み合わせる折り紙のようなイメージです。
コーチジョイントの利点は、繋ぎ目が頑丈になることです。鉄板同士がしっかりと噛み合うため、車体が歪んだり、振動したりしても簡単には外れません。また、溶接のように熱を加えないため、鉄板の材質が変化することが少なく、強度を保つことができます。さらに、リベット留めと比べて、繋ぎ目が滑らかになるため、空気抵抗を減らすことにも繋がります。
このコーチジョイントは、車だけでなく、電車や飛行機など、様々な乗り物に使われています。特に、軽くて強い構造が求められる乗り物には欠かせない技術です。近年では、鉄板だけでなく、アルミや樹脂など、異なる素材を繋ぎ合わせることも可能になっています。
このように、コーチジョイントは、様々な素材を繋ぎ合わせ、軽くて強く、美しい形を実現する、現代の乗り物作りには無くてはならない技術と言えるでしょう。