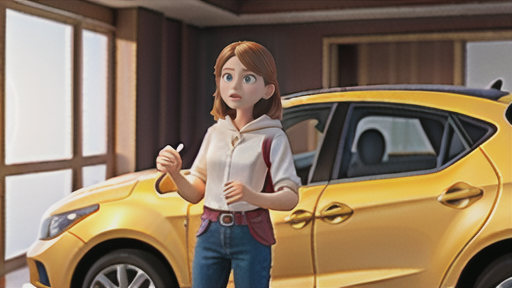
回転体のバランス調整:ダイナミックバランス試験機
車は、たくさんの部品が組み合わさって動いています。その中で、エンジンやタイヤのようにくるくる回る部品は、バランスがとれていることがとても大切です。バランスが少しでも崩れると、どうなるのでしょうか?
まず、振動が起きます。バランスの悪いコマを回すと、ブルブルと震えるのと同じです。車では、この振動が大きくなり、車全体が揺れてしまいます。そうなると、乗り心地が悪くなり、長時間運転していると疲れてしまうでしょう。また、騒音も発生します。振動が周りの空気を震わせ、不快な音を出すのです。ゴーという音や、ガタガタという音が大きくなり、静かな車内空間は保てません。
さらに、部品の寿命にも影響します。振動によって部品同士がこすれ合い、摩耗が早まります。部品が早く傷んでしまうと、交換する回数が増え、費用もかかります。
もっと怖いのは、重大な故障につながる可能性もあることです。例えば、高速で回転しているタイヤのバランスが崩れると、タイヤが破損してしまうかもしれません。これは大変危険なことです。
では、どのようにして回転体のバランスを整えているのでしょうか?回転体のバランスを精密に調整する専用の機械があります。この機械は「回転体の均衡測定器」と呼ばれ、回転体のわずかな重さの偏りも見つけることができます。そして、その偏りを修正することで、スムーズな回転を実現します。この作業のおかげで、私たちは快適に、そして安全に車に乗ることができるのです。回転体のバランス調整は、車の性能と安全を守る上で、なくてはならない工程なのです。