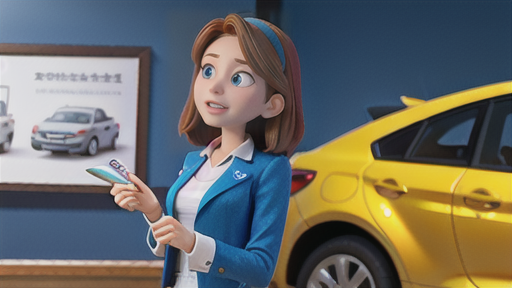
進化する車のガスケット技術
車はたくさんの部品が組み合わさってできています。それぞれの部品が正しく働くことで、車はスムーズに走ることができます。部品同士のつなぎ目には、隙間がどうしてもできてしまいます。この隙間から、液体や気体が漏れてしまうと、車がうまく動かなくなってしまいます。このような漏れを防ぐために重要な役割を果たしているのが、ガスケットです。
ガスケットは、例えるなら、家の窓枠とガラスの隙間を埋めるパテのようなものです。つなぎ目の隙間をしっかりと埋めて、液体や気体が漏れないようにします。車のエンジンは、高い圧力と温度の中で動いています。そのため、ガスケットは、これらの厳しい環境にも耐えられるように作られています。
ガスケットの材料には、ゴムや金属、樹脂など、様々なものが使われています。それぞれの部品の役割や、設置される場所の環境に応じて、最適な材料が選ばれます。例えば、エンジンのヘッドガスケットは、高温高圧にさらされるため、金属や特殊な繊維を組み合わせた、丈夫なものが使われます。一方、オイルパンのガスケットなどは、比較的低い圧力環境で使用されるため、ゴム製のものが使われることが多いです。
ガスケットが正しく機能しないと、様々な問題が発生する可能性があります。例えば、エンジンオイルや冷却水が漏れてしまうと、エンジンの性能が低下したり、最悪の場合、エンジンが壊れてしまうこともあります。また、排気ガスが漏れてしまうと、車に乗っている人の健康に悪影響を与える可能性もあります。
このように、ガスケットは小さいながらも、車の性能と安全を維持するために、非常に重要な役割を果たしています。そのため、ガスケットの素材や構造は、常に改良が重ねられています。より高い耐久性や耐熱性を持つガスケットが開発されることで、車の性能向上や環境保護にも貢献しています。