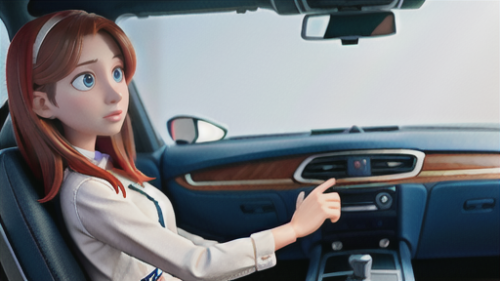
ワイパーブレード:車の視界を守る縁の下の力持ち
雨や雪、そして砂埃などの汚れから窓ガラスを守り、運転する人の視界を確保するのが窓拭きゴムの大切な役割です。安全な運転に欠かせない部品であり、適切な窓拭きゴム選びと日頃の手入れは、快適な運転を続ける上でとても大切です。
窓拭きゴムは、窓ガラスにぴったりくっついて汚れを拭き取るゴムの部分と、それを支える金属の部分でできています。このゴムの部分は、窓ガラスの曲面にぴったりと沿って、水滴や汚れを効率よく拭き取らなければなりません。ゴムの素材は、気温の変化や紫外線などによる劣化に強く、長期間にわたって性能を維持できるものが求められます。また、拭き取り性能を高めるために、撥水加工が施されたものや、細かい溝が刻まれたものなど、様々な種類があります。
金属の部分は、ゴムの部分をしっかりと固定し、窓拭き腕の動きに合わせて正確に動くように作られています。この金属の部分は、耐久性が高く、錆びにくい素材で作られていることが重要です。また、窓ガラスへの圧力を均一に保ち、拭きムラを発生させないような構造になっているかも重要な点です。
これらの部品が組み合わさって、運転する人のはっきりとした視界を確保し、安全な運転を支えています。窓拭きゴムは消耗品であり、定期的な交換が必要です。古くなった窓拭きゴムは、拭きムラや拭き残しを引き起こし、視界不良の原因となります。また、ガラスに傷をつける可能性もあるため、定期的な点検と交換を心掛けましょう。適切な窓拭きゴムを選び、きちんと手入れをすることで、安全で快適な運転を続けられます。