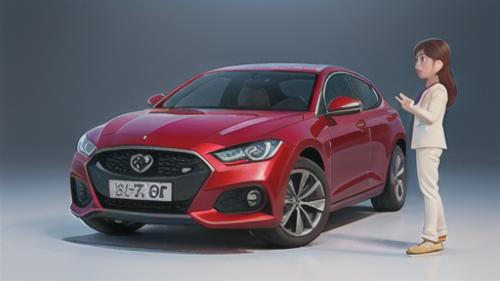
クルマのドアモジュール:その利点と将来
車のドアは、様々な部品が組み合わさってできています。これらの部品を一つ一つ組み立てるのは、手間と時間がかかります。そこで、ドア周りの部品をあらかじめ一つの部品にまとめておくのが、ドアモジュールです。
ドアモジュールには、窓の開閉を行う部品、鍵の開閉を行う部品、ドアを開けるための取っ手など、様々な機能部品が含まれています。窓を開け閉めする部品には、モーターやレールなどが組み込まれており、スイッチ一つでスムーズに窓を動かすことができます。また、鍵の開閉を行う部品には、電気仕掛けで動くものや、従来の手動式のものなど、様々な種類があります。さらに、ドアの内側には、腕を置くためのひじ掛けや、ドアを閉める時に掴む取っ手、音楽を聴くためのスピーカーなども取り付けられています。これらの部品は、ドアの内張りに合わせてデザインされ、快適な車内空間を作り出しています。
ドアモジュールには、これらの部品だけでなく、電気配線も含まれています。配線は、それぞれの部品へ電気を供給するために必要不可欠なものです。ドアモジュールでは、これらの配線が予めまとめて整理されているため、車体への取り付けが容易になります。
このように、ドアモジュールは、多くの部品を一つにまとめることで、車の組み立てを簡単にするだけでなく、製造の効率化にも貢献しています。部品メーカーがドアモジュールを完成させて完成車メーカーに納品することで、完成車メーカーは、ドア周りの部品を一つずつ取り付ける手間を省くことができます。結果として、製造コストの削減や、組み立て時間の短縮につながり、より良い車をより早く提供することが可能になります。