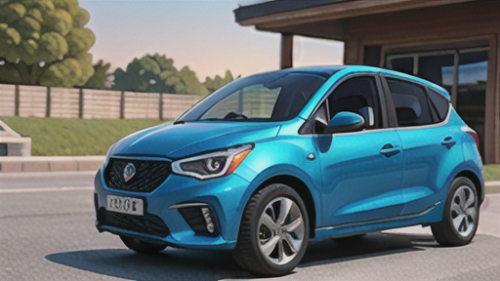
電気でつなぐ!スポット溶接のひみつ
spot溶接は、金属と金属をくっつける技の一つで、電気の力を借りて金属を溶かし合わせます。まるでホッチキスの針のように、点と点で留めるため、「spot溶接」と呼ばれています。
spot溶接を行うには、まず溶接したい箇所に電極という金属の棒を押し当てます。そして、電極を通じて電気を流すと、金属には電気の通りにくさ(抵抗)があるため、その部分に熱が発生します。この熱(抵抗熱)を利用して金属を溶かし、冷えて固まると、二つの金属がしっかりとくっつきます。
この方法は、薄い鉄板を繋げるのに向いており、特に自動車の車体作りで広く使われています。自動車の車体は、たくさんの薄い鉄板を組み合わせて作られていますが、spot溶接を使うことで、これらの鉄板を素早く、かつしっかりと繋げることができます。
spot溶接は、他の溶接方法に比べて、作業時間が短く、費用も抑えることができます。そのため、一度にたくさんの製品を作る大量生産に向いています。また、点と点で溶接するため、熱の影響を受ける範囲が狭く、金属の変形も少なく抑えることができます。
spot溶接された部分は、高い強度を持ち、簡単には外れません。そのため、強度が求められる自動車の車体作りに適していると言えるでしょう。spot溶接は、自動車だけでなく、家電製品や建材など、様々な製品の製造に使われており、現代のモノづくりになくてはならない技術となっています。