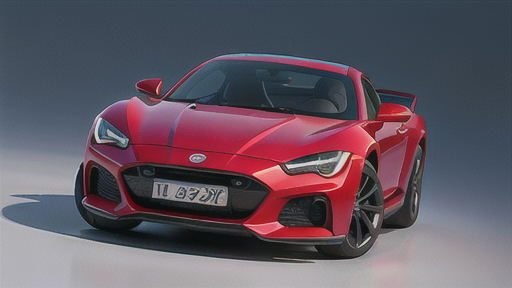
型の設計:アンダーカットを理解する
物を造るには、材料を流し込んで固める型が必要です。この型は、完成品の形状を反転させたもので、材料を流し込んで固めた後に型から取り外して製品を完成させます。
型から製品をきれいに取り外すためには、型の設計が重要です。製品の形によっては、型から取り外すのが難しい場合があります。例えば、製品にくぼみや出っ張りがあると、型から外す際に引っかかってしまうことがあります。このような、型から製品を取り外す際に邪魔になる部分を「切り下げ」と呼びます。「切り下げ」があると、製品が型から外れなくなったり、製品や型が壊れたりする可能性があります。
製品の設計段階から「切り下げ」をなくす工夫をすることが大切です。「切り下げ」を避けるには、製品の形状を工夫する方法があります。例えば、出っ張りを小さくしたり、傾斜を緩やかにしたりすることで、「切り下げ」をなくすことができます。また、型の分割方法を工夫する方法もあります。型を複数のパーツに分割することで、「切り下げ」がある部分もスムーズに取り外せるようになります。例えば、複雑な形状の製品を造る場合は、型を上下左右のパーツに分割し、それぞれのパーツを組み合わせることで製品を成形します。
「切り下げ」をなくすことで、製品を型からスムーズに取り外すことができ、生産効率を高めることができます。また、製品や型の破損を防ぐことができ、高品質な製品を安定して供給することに繋がります。製品の設計段階で「切り下げ」を考慮することで、無駄なコストや時間を削減し、より良い製品を造ることができます。