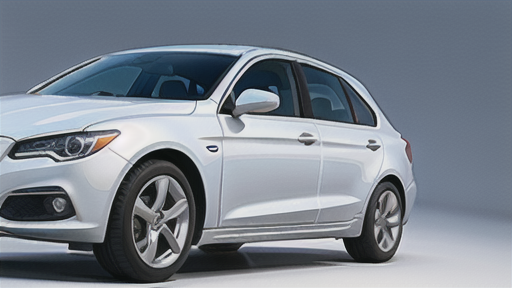
車の骨格:冷間圧延鋼板
鉄を薄く延ばした板状の素材である鋼板は、自動車の車体を作る上で欠かせない材料です。鋼板には大きく分けて、熱間圧延鋼板と冷間圧延鋼板の二種類があります。
熱間圧延鋼板は、高い温度で圧延されます。高温で加工するため、材料の変形抵抗が少なく、比較的低い力で圧延できます。このため、製造にかかる費用を抑えることができ、製造コストが低いという利点があります。しかし、高温での加工は、表面の酸化や粗さが発生しやすく、寸法精度も低くなる傾向があります。そのため、高い寸法精度や表面の滑らかさが求められる部分にはあまり使われません。主に、強度が必要とされる骨格部分やホイールなどに用いられます。
一方、冷間圧延鋼板は、熱間圧延鋼板をさらに常温で圧延することで製造されます。常温で圧延することで、表面が滑らかで美しくなり、寸法精度も高くなります。また、加工によって材料の強度が増すため、薄くても高強度な鋼板を作ることが可能です。冷間圧延鋼板は、表面の美しさと加工のしやすさから、自動車の外板などに用いられます。複雑な形状に成形しやすく、美しい塗装を施すことができるため、自動車のデザイン性を高める上で重要な役割を果たしています。
このように、熱間圧延鋼板と冷間圧延鋼板は、それぞれ異なる特性を持っています。自動車メーカーは、部品の求められる性能やコストなどを考慮し、それぞれの特性に合わせて鋼板を使い分け、安全で美しい自動車を作り上げています。また、近年では、これらの鋼板に加えて、さらに高度な特性を持つ高張力鋼板や超高張力鋼板なども開発され、自動車の軽量化や安全性の向上に貢献しています。