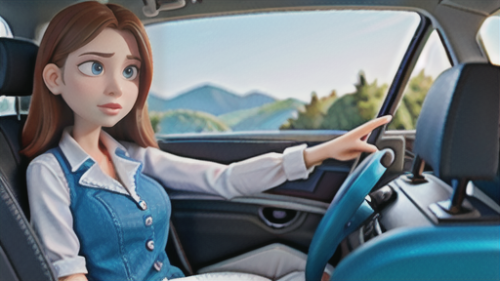
中心穴研削:高精度部品を生み出す技
機械部品を作る上で、中心穴は大切な役割を担っています。中心穴とは、部品の両端に開けられた小さな穴のことです。特に、旋盤や研削盤といった回転する機械で長い部品を加工する際に、この中心穴が大きな力を発揮します。
中心穴には、部品の回転軸を正しく定めるという重要な役割があります。部品を機械に固定する際に、この中心穴に固定具の先端を差し込みます。これにより、部品の中心軸が機械の回転軸とぴったり一致し、部品がぶれることなく回転するのです。中心穴がなければ、部品が振動したり、中心からずれて回転したりして、正確な加工ができません。
中心穴があることで、安定した支持も得られます。長い部品を回転させると、遠心力や加工時の力によって部品が曲がってしまうことがあります。しかし、中心穴に固定具を差し込むことで、部品をしっかりと支え、変形を防ぐことができます。これにより、高い精度での加工が可能になります。
中心穴がない場合、部品の振れや偏心が発生し、加工精度が低下するだけでなく、工具の寿命にも悪影響を及ぼす可能性があります。例えば、部品の外周を削る際に、部品がぶれていれば、削りムラが生じたり、工具が早く摩耗したりします。自動車部品のように高い精度が求められる部品では、中心穴の精度は製品全体の品質に直結します。
中心穴の研削は、非常に重要な工程です。中心穴の形状や寸法精度が、加工精度や製品の品質を左右します。そのため、中心穴の研削には、専用の研削盤や高度な技術が用いられます。適切な中心穴の研削を行うことで、部品の安定した回転と高精度な加工を実現し、高品質な製品を作り出すことができるのです。