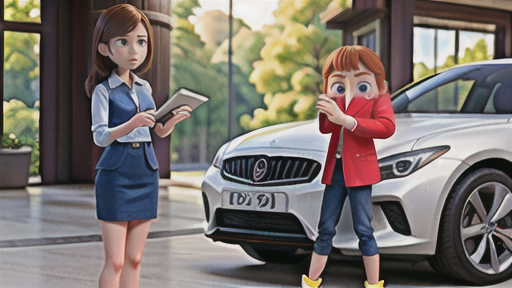
車の製造における熱圧縮加工
熱圧縮加工とは、読んで字のごとく、材料を加熱しながら圧力を加えて成形する技術です。高温で材料を柔らかくすることで、複雑な形にも容易に変形させることができます。この方法は、自動車の部品作りにおいて、強度と軽さを両立させる上で欠かせない役割を担っています。
熱圧縮加工には様々な種類があり、熱間鍛造や熱間圧延などが代表的です。熱間鍛造は、加熱した金属材料を金型で挟み込み、強い力でプレスして成形する方法です。これにより、非常に高い強度と耐久性を持つ部品を作ることができます。例えば、エンジンのクランクシャフトやコネクティングロッドなど、過酷な環境で使用される部品に多く用いられています。一方、熱間圧延は、加熱した金属材料を回転するローラーの間を通すことで、板状や棒状に成形する方法です。薄いながらも強度のある部品を効率的に製造できるため、ボディパネルやサスペンション部品などに利用されています。
熱圧縮加工を行う際には、材料の選定が重要です。高温での加工に耐えられる材料でなければ、変形が不均一になったり、割れが生じたりする可能性があります。また、温度管理も非常に重要です。適切な温度範囲で加工を行うことで、材料の変形を制御し、目的の形状や特性を得ることができます。温度が高すぎると材料が溶けてしまったり、低すぎると変形しにくくなったりするため、熟練した技術者による緻密な調整が必要です。さらに、圧力のかけ方も重要です。圧力が均一にかかっていないと、部品の形状が歪んだり、強度が低下したりする可能性があります。
このように、熱圧縮加工は、高度な技術とノウハウが必要な加工方法です。熟練の技術者たちが長年の経験と知識を活かし、材料の選定、温度管理、圧力のかけ方を緻密に制御することで、高精度で高品質な部品を日々製造しています。熱と圧力の絶妙なバランスによって、自動車の性能と安全性を支えていると言えるでしょう。