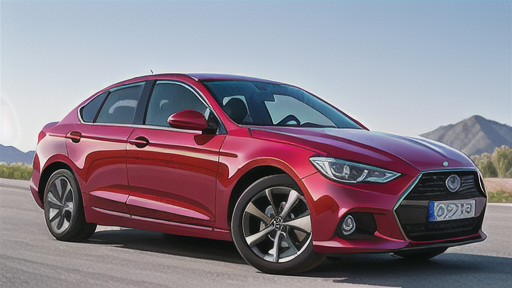
左右非対称のデザイン:クラウンスーツ
車は左右対称が当然の姿と思われてきました。確かに、道の真ん中を走る以上、空気抵抗を減らすには左右対称である方が合理的です。そのため、車の正面、側面、背面、どこを見ても左右対称のデザインが主流でした。しかし、近年、この常識を覆す車が登場しました。トヨタの「クラウンスーツ」です。この車は、左右で異なる色や模様を取り入れた、大胆な非対称デザインを採用しています。まるで、色の異なる布を繋ぎ合わせた衣装をまとっているかのようです。
この斬新なデザインは、見る人に驚きと強い印象を与えます。例えば、片側を落ち着いた黒でまとめ、もう片側を鮮やかな赤で彩ることで、車の二面性を表現しています。静と動、陰と陽、相反する二つの要素が一つの車に共存することで、他に類を見ない独特な魅力が生まれます。また、左右で異なる模様を取り入れることで、車の個性をさらに際立たせることも可能です。例えば、片側に流れるような曲線模様を施し、もう片側には幾何学模様を配置することで、優雅さと力強さを同時に表現できます。
左右非対称のデザインは、単なる奇抜さを狙ったものではありません。左右それぞれのデザインが持つ個性を際立たせ、それらを調和させることで、美しさや力強さなど、新たな魅力を引き出しているのです。左右非対称のデザインは、車のデザインにおける新たな可能性を示唆しています。今後、ますます多くの車が、この大胆なデザインに挑戦していくことでしょう。左右非対称のデザインは、もはや奇抜な例外ではなく、車の新たな表現方法として確立されつつあります。