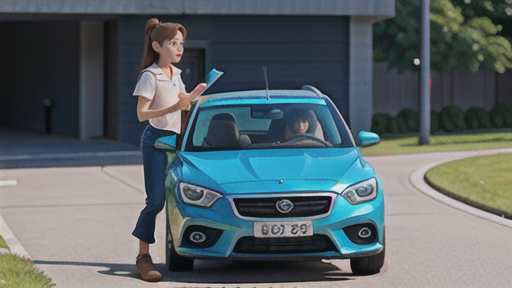
鋳鉄:自動車を支える縁の下の力持ち
鋳鉄とは、鉄に炭素を多く含ませた合金です。炭素の割合は、1.7%から6.7%と高く、これが鋳鉄の特徴的な性質を生み出しています。一般的な鋼は炭素含有量が2%以下であるのに対し、鋳鉄はそれよりもはるかに多くの炭素を含んでいるため、鋼とは異なる性質を示します。
まず、炭素の含有量が多いことで、鋳鉄は溶けやすいという性質を持ちます。鉄は単体では溶ける温度、つまり融点が非常に高いのですが、炭素を混ぜることで融点が下がります。これは、溶かした金属を型に流し込んで製品を作る鋳造に適しています。高い温度で溶かす必要がないため、製造工程が簡略化され、エネルギー消費も抑えられます。
また、溶けた鋳鉄は流れやすいため、複雑な形状の型にも入り込みやすいという利点があります。そのため、複雑な部品を製造する場合でも、鋳鉄は隅々まで流れ込み、正確な形状を再現できます。細かい装飾や複雑な模様なども、鋳鉄を用いることで綺麗に作り出すことが可能です。
さらに、鋳鉄は強度と硬度が高いという特徴も持っています。これは、炭素が鉄の結晶構造に影響を与えることで生まれます。炭素が多いことで、鉄の結晶構造が変化し、硬くて丈夫な材料となるのです。
このように、鋳鉄は溶けやすさ、流れやすさ、強度と硬度を兼ね備えた材料であるため、古くから様々な用途に用いられてきました。例えば、水道管やマンホールの蓋、エンジンブロックやブレーキ部品など、私たちの生活を支える多くの製品に鋳鉄が利用されています。近年では、製造技術の進歩により、より精密な鋳造が可能となり、さらに幅広い分野での活用が期待されています。