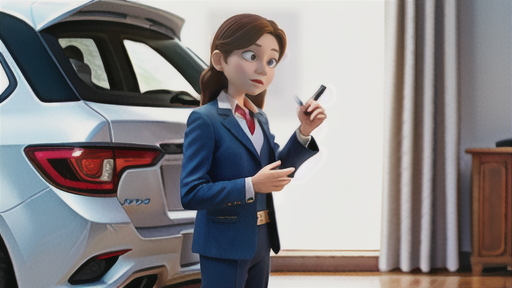
部品調達:車の心臓部を作る
車は、小さなネジから大きなエンジンまで、数万点もの部品が組み合わさってできています。これらの部品を、必要な時に、必要な数だけ集めるのが部品調達の仕事です。部品調達は、いわば車の製造現場における血液循環のようなもので、一つでも部品が欠ければ車は完成しません。
部品調達では、まずどの会社からどの部品を買うのかを決めます。多くの部品メーカーの中から、品質、価格、納期などを考慮して最適な会社を選びます。品質が低い部品を使ってしまうと、車の安全性や性能に問題が生じる可能性があります。また、価格が高すぎると車の製造コストが上がってしまい、買い求めやすい車を作ることが難しくなります。さらに、部品が納期通りに届かないと、工場の生産ラインが止まってしまい、多くの損失が出てしまいます。そのため、部品調達担当者は、まるで指揮者のように、様々な要素を考慮しながら多くの部品メーカーとやり取りを行います。
部品の注文後は、きちんと期日通りに届くように管理するのも大切な仕事です。部品メーカーとの連絡を密に取り、製造の進捗状況や輸送状況を常に確認します。天候不順や世界情勢の変化など、予期せぬ出来事が発生した場合でも、柔軟に対応し、部品が滞りなく工場に届くように調整します。部品調達は、単に部品を集めるだけでなく、安定した生産を支える重要な役割を担っています。そして、高品質な部品を適切な価格で、決められた期日までに調達することで、良い車を効率よく作ることができるのです。まさに、部品調達は車作りを支える縁の下の力持ちと言えるでしょう。