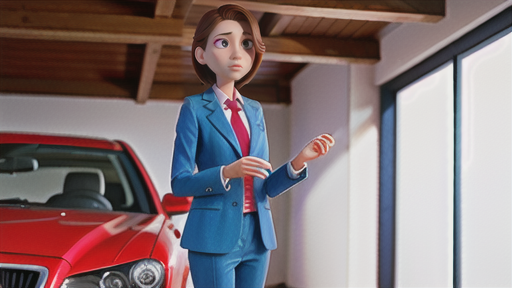
車の性能を支える清浄技術
車は、たくさんの部品が組み合わさって動いています。小さなネジから大きな車体まで、それぞれの部品が重要な役割を担っています。これらの部品の中には、非常に精密に作られたものや、わずかな隙間で動くものもたくさんあります。時計の歯車のように、複雑に噛み合って動いている部分もあるのです。
このような精密な部品にとって、目に見えないほどの小さなごみでさえ、大きな問題を引き起こす可能性があります。例えば、車の心臓部であるエンジンや、動力の伝達を担う変速機の内部には、多くの摺動部が存在します。これらの摺動部に、塵や埃などのごみが混入すると、部品同士が擦れ合う際に、まるでやすりのように摩耗を促進させてしまいます。結果として、部品の寿命が短くなり、車が本来の性能を発揮できなくなるばかりか、予期せぬ故障につながる恐れもあるのです。
特に、自動変速機のコントロールバルブボディは、非常に小さなバルブで油圧を制御しているため、ごみに非常に敏感です。もし、ごみがバルブに詰まってしまうと、油圧制御がうまくいかなくなり、変速不良や故障の原因となります。スムーズな加速や減速ができなくなったり、最悪の場合、車が動かなくなってしまうこともあります。
そのため、車の性能を維持し、長く乗り続けるためには、部品の清浄さを保つことが何よりも重要になります。これは、工場での製造段階から、部品を組み立てる段階、そして、完成した車を整備する段階まで、すべての過程において、徹底的に管理されなければなりません。日頃から、車内を清潔に保つことも大切です。一見、大したことがないように見える小さなごみも、積み重なれば、やがて大きな問題を引き起こす可能性があるため、清浄さへの意識を高く持つことが不可欠です。