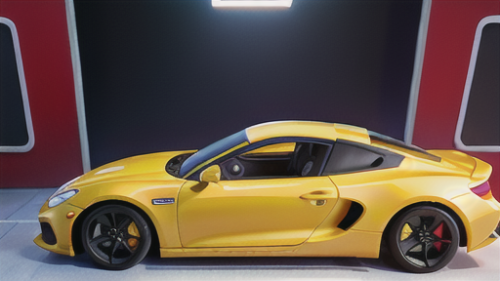
車の安全性とせん断応力
自動車の車体は、走行中に様々な力を受けます。平坦でない道路を走る際の衝撃や、曲がりくねった道を走行する時に生じる遠心力、そして万が一の衝突の際の衝撃など、これらは車体に複雑な力を加えます。これらの力の中で、車体を横切るように働く力が「せん断応力」です。これは、まるで鋏で紙を切るように、物体をずらして変形させようとする力です。
せん断応力は、車体の構造強度を保つ上で非常に大切な役割を担っています。もし車体がせん断応力に耐えられなければ、車体は歪んだり、最悪の場合は破断してしまう可能性があります。そのため、自動車の設計者は、車体が様々な状況下で発生するせん断応力に耐えられるように、様々な工夫を凝らしています。
車体の骨組みを構成する材料の選択は、せん断応力への耐性を高める上で非常に重要です。例えば、高い強度を持つ鋼板を使うことで、車体の強度を高めることができます。また、車体の骨組みの形状も重要です。最適な形状にすることで、せん断応力が集中するのを防ぎ、車体全体で力を分散させることができます。
近年の自動車設計では、コンピューターを用いたシミュレーション技術が広く活用されています。様々な走行状況を想定し、車体にどのようなせん断応力がかかるかを事前に予測することで、より安全で効率的な車体構造を設計することが可能になっています。これらの技術により、乗る人の安全を確保すると同時に、車体の軽量化も実現しています。軽い車体は燃費の向上に繋がり、環境負荷の軽減にも貢献します。このように、せん断応力への対策は、自動車の安全性、燃費性能、そして環境性能を高める上で、極めて重要な要素と言えるでしょう。