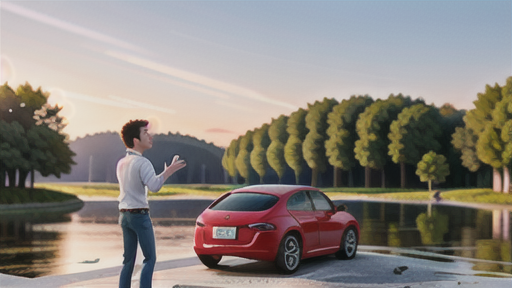
隠れた機能美:モヒカンルーフの秘密
車の世界には、聞きなれない表現がたくさんあります。その一つに「モヒカン屋根」という言葉があります。この言葉は、車の屋根の形を表す表現で、一体どんな屋根なのか、興味をそそられますよね。
この名前の由来は、屋根の両端にある雨どい構造にあります。雨どいは、屋根に降った雨水を集めて排水するための溝ですが、この雨どいの配置がモヒカン屋根の独特な形状を生み出しているのです。屋根の中央部分は雨どいがなく、両端にだけ雨どいが設置されています。このため、横から見ると、中央部分が盛り上がって両端が低くなっているように見えます。この形状が、まるでモヒカン刈りの髪型のように見えることから、「モヒカン屋根」と呼ばれるようになりました。
一見風変わりな名前に思えますが、形を思い浮かべると、なるほどと納得できるネーミングです。そして、この独特な形は、見た目だけでなく、様々な利点も持っています。雨どいを両端に寄せることで、屋根の中央部分を広く使うことができます。これにより、車内の空間を広げたり、開放感を高めたりすることが可能になります。また、屋根の強度を高める効果もあると言われています。
このように、モヒカン屋根は、変わった名前の由来とその機能性の両方で、私たちを魅了する車の屋根形状の一つと言えるでしょう。単なるデザイン上の特徴ではなく、実用性も兼ね備えている点が、モヒカン屋根が多くの車に採用されている理由と言えるのではないでしょうか。