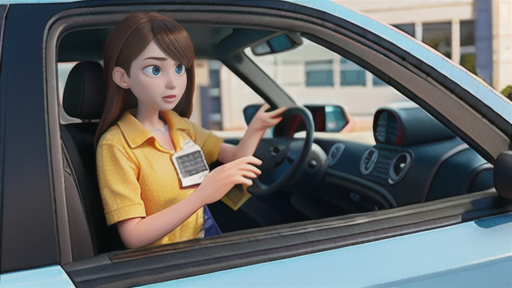
車の組み立て精度:公差の重要性
車は、数万点もの部品を組み合わせて作られています。一つ一つの部品の寸法や取り付け位置が、全体の性能や品質に大きな影響を与えます。そこで重要になるのが「組み立て公差」です。組み立て公差とは、それぞれの部品を組み合わせる際に、寸法や位置がどれくらいずれても許されるのかを示す範囲のことです。
例えば、エンジンのピストンとシリンダーを考えてみましょう。ピストンはシリンダーの中を上下に動いて力を生み出しますが、この二つの部品の間には、わずかな隙間が必要です。この隙間が狭すぎると、ピストンがシリンダーに接触して動きにくくなり、焼き付きを起こしてしまうかもしれません。逆に隙間が広すぎると、圧縮された混合気が漏れ出してしまい、エンジンの力が十分に出なくなります。そこで、ピストンとシリンダーの隙間は、あらかじめ決められた範囲内に収まるように設計・製造されます。これが組み立て公差の一例です。
また、車体の骨格を形成するフレームにも、組み立て公差が重要な意味を持ちます。フレームは、車の強度や走行安定性、衝突安全性などを左右する重要な部品です。フレームを構成する部品の位置や寸法がずれていると、車体が歪んだり、強度が低下したりする可能性があります。走行中に振動が発生しやすくなったり、衝突時に適切な衝撃吸収ができなくなったりする危険性も高まります。
このように、組み立て公差は、車の性能や安全性を確保するために欠かせない要素です。設計段階で適切な公差を設定し、製造工程においてもその公差を厳守することで、高品質で安全な車を作ることができるのです。