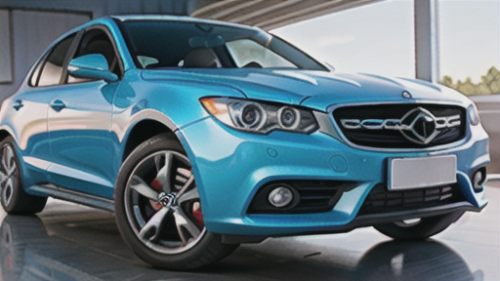
車のタイヤコード:進化の歴史と種類
車は地面と接するタイヤによって支えられ、その動きを制御されています。このタイヤの性能を大きく左右するのが、タイヤコードと呼ばれる内部構造です。タイヤコードとは、タイヤの骨格を形作る、いわばタイヤの骨組みのようなものです。タイヤは、何層にも重ねられたゴムの層でできていますが、このゴムの層と層の間にタイヤコードが織り込まれています。
タイヤコードは、タイヤの強度と形状を保つという重要な役割を担っています。車が走行する際には、車両の重さや路面からの衝撃など、様々な力がタイヤにかかります。タイヤコードは、これらの力に耐え、タイヤが変形したり破損したりするのを防ぎます。また、タイヤコードはタイヤの形を安定させることで、スムーズな走行と燃費の向上にも貢献しています。
タイヤコードの素材は時代と共に変化してきました。初期のタイヤは、木綿を素材としたコードが使われていました。しかし、木綿は強度が十分ではなく、耐久性にも問題がありました。その後、技術の進歩により、様々な人工繊維や金属線が開発され、現在ではこれらの素材が主流となっています。人工繊維の中でも、レーヨン、ナイロン、ポリエステル、アラミド繊維などは、高い強度と耐久性、そして耐熱性を備えているため、多くのタイヤに使用されています。また、鋼線は非常に高い強度を持ち、大型車や重量のある貨物車を支えるタイヤに利用されています。
このように、タイヤコードは種類によって特性が異なり、使用する車の種類や用途に合わせて最適な素材が選ばれています。例えば、乗用車には、乗り心地と燃費性能を重視したタイヤコードが、高速走行するスポーツカーには、より高い強度と耐久性を持つタイヤコードが、大型トラックやバスには、重い荷物を支えるための非常に強いタイヤコードが使用されています。タイヤコードは目に見えない部分ですが、車の安全性と性能を左右する重要な部品なのです。