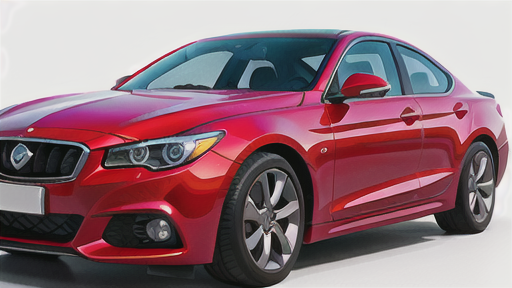
車の部品を支える熱硬化性樹脂
熱硬化性樹脂は、加熱することで固まるプラスチックの一種です。一度固まると、再び熱しても柔らかくならず、形を変えることができません。この性質は、熱可塑性樹脂とは大きく異なります。熱可塑性樹脂は、熱すると柔らかくなり、冷やすと固まる性質を持ち、何度も形を変えることができます。例えるなら、熱可塑性樹脂はお餅のようなものです。加熱すると柔らかく伸び、冷やすと再び固まります。一方、熱硬化性樹脂は卵のようなものです。生の卵は液体ですが、加熱すると固まります。そして、一度固まった卵は再び液体には戻りません。
熱硬化性樹脂はこのような性質を持つため、様々な用途で使われています。例えば、電気製品の部品や自動車の部品、建材などに利用されています。熱や衝撃に強く、耐久性に優れているため、過酷な環境で使われる製品に適しています。また、複雑な形状に成形できることも利点の一つです。
しかし、熱硬化性樹脂は一度固まると形を変えることができないため、リサイクルが難しいという課題もあります。熱可塑性樹脂のように、加熱して溶かして再利用することができないため、廃棄物処理の問題が生じる可能性があります。このため、近年では、リサイクルしやすい材料の開発や、再利用方法の研究が進められています。また、製品の寿命を長くすることで、廃棄物の発生量を減らす取り組みも重要です。熱硬化性樹脂は優れた特性を持つ一方、環境への影響も考慮しながら、適切に利用していく必要があります。