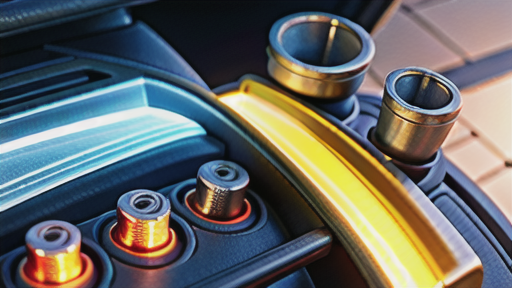
高性能の証!アルミ鍛造ピストン
自動車の心臓部であるエンジンの中で、ピストンはなくてはならない部品です。ピストンの役割は、エンジン内部に取り込まれた混合気を圧縮し、爆発によって生じた力をクランクシャフトに伝えることです。この一連の動作を繰り返すことで、車は前に進むことができます。
ピストンには様々な種類がありますが、高性能エンジンや競技用エンジンには、より高い強度と耐久性が求められます。そこで採用されるのがアルミ鍛造ピストンです。
アルミ鍛造ピストンは、その名の通りアルミ合金を材料として作られます。しかし、一般的なアルミ合金部品のように型に流し込んで作るのではなく、高温に加熱したアルミ合金に強力な圧力をかけて成形する「鍛造」という製法を用います。鍛造を行うことで、金属内部の組織が細かくなり、密度が高まります。この緻密な構造こそが、アルミ鍛造ピストンの強さの秘密です。
鋳造という型に流し込む製法で作ったピストンと比べると、鍛造ピストンは強度と耐熱性に優れているという特徴があります。エンジンの内部は高温・高圧という過酷な環境です。そのため、ピストンには高い強度と耐熱性が求められます。アルミ鍛造ピストンは、この過酷な環境に耐えうる性能を備えているため、高性能エンジンに最適な部品と言えるでしょう。
高回転・高出力といった高性能エンジンの心臓部を支えているのが、この小さなアルミ鍛造ピストンです。高い強度と耐久性を持つアルミ鍛造ピストンは、自動車の進化を支える重要な部品の一つと言えるでしょう。