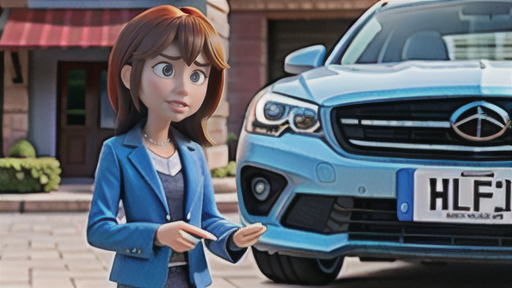
閉塞鍛造:高精度な自動車部品製造技術
閉塞鍛造とは、金属を型に閉じ込めて圧力をかけることで、複雑な形をした部品を作り出す鍛造技術のひとつです。
普通の型鍛造では、金属が型からはみ出る部分(バリ)をあえて作って、型全体に金属を詰めることで製品の形を作ります。このバリは後工程で除去する必要があります。しかし、閉塞鍛造では、バリの出口がない型を使います。そのため、金属は型の中に完全に閉じ込められた状態で形作られます。
閉塞鍛造の大きな利点は、材料の無駄を減らせることです。バリが出ないため、材料を余すことなく使うことができます。これは、材料費の削減につながり、環境負荷の低減にも貢献します。また、金型全体に均等に圧力がかかるため、製品の寸法精度が非常に高くなります。複雑な形や細かい部分まで正確に再現でき、表面も滑らかに仕上がります。さらに、材料の内部組織が緻密になるため、製品の強度や耐久性が向上します。
閉塞鍛造は、自動車部品の製造で広く使われています。例えば、エンジンの部品やトランスミッションの部品、サスペンションの部品など、高い強度と精度が求められる部品に適しています。他にも、航空機部品や産業機械部品、建設機械部品など、様々な分野で活用されています。近年では、材料技術や加工技術の進歩により、さらに複雑で高精度な部品の製造が可能になってきており、閉塞鍛造の需要はますます高まっています。