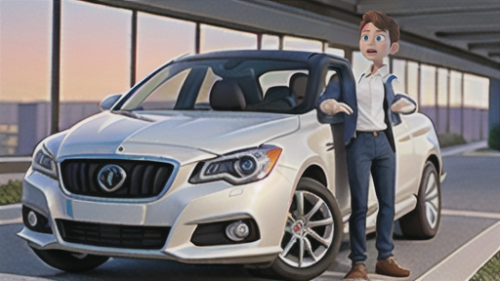
ピニオンギヤ諸元の深掘り解説
車はたくさんの部品が集まってできています。その中で、動力を伝えるための歯車は大切な役割をしており、ピニオン歯車と呼ばれる歯車は特に重要です。ピニオン歯車は、回転運動の向きを変えたり、回転の速さを変えたりするのに欠かせません。この文章では、ピニオン歯車の細かい特徴について説明し、その大切さについて深く考えていきます。
ピニオン歯車は、かみ合う歯車のうち、小さい方の歯車を指します。多くの場合、大きな歯車(ギヤ)と組み合わされて使われ、動力の伝達を行います。回転運動を伝えるだけでなく、回転速度や回転の力を変えることも可能です。例えば、エンジンの動力をタイヤに伝える際に、ピニオン歯車と大きな歯車を組み合わせることで、エンジンの速い回転をタイヤのゆっくりとした回転に変え、大きな力を生み出すことができます。
ピニオン歯車の重要な特徴の一つに「歯数」があります。歯数は、歯車の歯の数を表すもので、かみ合う歯車の歯数比によって回転速度の変換比率が決まります。歯数が少ないピニオン歯車は、大きな歯車と組み合わせることで、回転速度を大きく落とすことができます。逆に、歯数の多いピニオン歯車では、回転速度の変化は小さくなります。
ピニオン歯車の材質も重要です。歯車は常に回転し、大きな力に耐えなければならないため、強度と耐久性が求められます。そのため、ピニオン歯車には、硬くて摩耗しにくい鋼鉄がよく使われます。また、表面処理を施すことで、さらに強度や耐久性を高める工夫がされています。
ピニオン歯車の形も様々です。平歯車、はすば歯車、かさ歯車など、用途に合わせて様々な形状のピニオン歯車が設計されています。例えば、かさ歯車は、回転軸が交わる場合に用いられ、回転方向を90度変えることができます。
ピニオン歯車の細かい特徴を理解することは、車の性能や寿命を理解する上で非常に大切です。複雑な仕組みですが、一つずつ丁寧に理解していくことで、車の動きをより深く知ることができます。そして、ピニオン歯車は車の動力を伝えるという重要な役割を担っていることを改めて認識できるでしょう。