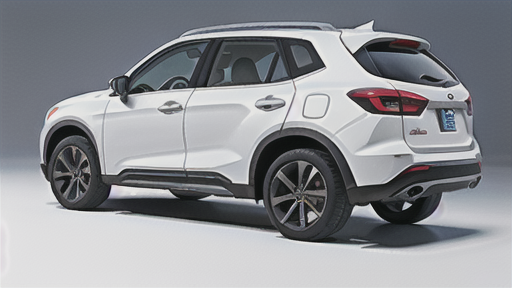
車の軽量化を実現するマグネシウム
車は、軽ければ軽いほど燃費が良くなります。そのため、車を作る人は、少しでも軽くするために様々な工夫をしています。昔から車作りに使われてきた鉄や、軽い金属として知られるアルミニウムなども、もちろん重要な材料です。しかし、近年、さらに軽い金属として注目を集めているのがマグネシウムです。マグネシウムは、アルミニウムと比べて3割ほど軽く、鉄と比べると4分の1ほどの重さしかありません。
このマグネシウムの軽さは、車の燃費を良くするために非常に役立ちます。車体が軽くなると、同じ距離を走るにも必要な燃料の量が少なくて済みます。例えば、重い荷物を積んだトラックは、空のトラックよりも多くの燃料を使います。同じように、車体が軽いほど、少ない燃料で走ることができるのです。また、車体が軽いと、加速性能も向上します。アクセルを踏んだ時に、車がより速くスピードを上げることができるようになります。さらに、ハンドリング性能も向上し、カーブを曲がるときなどもスムーズに運転できるようになります。これらの要素が組み合わさることで、より快適な運転を楽しむことができるようになります。
マグネシウムの利点は軽さだけではありません。マグネシウムはリサイクルしやすいという、環境にも優しい特徴も持っています。使い終わったマグネシウムの部品は回収され、溶かして再び新しい部品へと作り変えることができます。資源を無駄にすることなく、繰り返し使うことができるため、環境への負担を減らすことにも繋がります。このように、マグネシウムは車の軽量化に役立ち、燃費向上、加速性能やハンドリング性能の向上に貢献するだけでなく、環境にも優しい、未来の車作りにとって重要な材料と言えるでしょう。