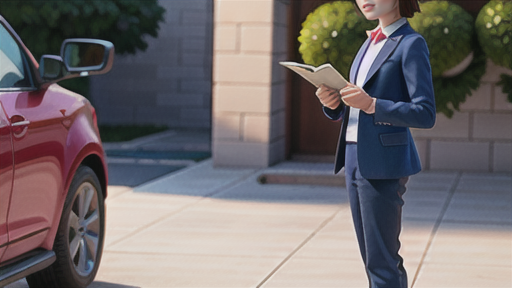
車の軽量化を実現する積層射出成形
車は、私たちの生活に欠かせないものとなっています。移動手段としてだけでなく、荷物を運んだり、趣味を楽しんだりなど、様々な用途で使われています。しかし、車の利用は燃料を消費するため、環境への影響も無視できません。地球温暖化対策としても、家計の負担を軽くするためにも、燃費を良くすることは大変重要な課題です。
燃費を良くする、つまり少ない燃料で長い距離を走るためには、車の重さを軽くすることが最も効果的です。重い車は動かすために多くのエネルギーが必要になるため、燃費が悪くなります。反対に、軽い車は少ないエネルギーで動かすことができるため、燃費が良くなります。
このため、各自動車製造会社は車の様々な部品を軽くするための技術開発に力を入れています。車体を軽くするための方法はいくつかありますが、近年注目を集めている技術の一つが積層射出成形です。これは、異なる種類のプラスチックを層状に重ねて成形する技術です。
従来のプラスチック成形では、単一の材料しか使用できませんでしたが、積層射出成形では、強度が高い材料と軽い材料を組み合わせることで、強度を保ちながら軽量化を実現できます。例えば、車のバンパーなどは、強い衝撃に耐える必要があるため、強度が高い材料で作られています。しかし、強度が高い材料は一般的に重いため、燃費に悪影響を与えます。積層射出成形を用いることで、表面には強度が高い材料を、内部には軽い材料を使うことができます。これにより、強度を落とすことなく軽量化することが可能になり、燃費向上に大きく貢献します。
積層射出成形は、他にも様々な部品への応用が期待されています。例えば、車の内装部品やエンジン部品などにも利用することで、更なる軽量化と燃費向上を実現できる可能性を秘めています。この技術の進歩は、環境保護と家計への負担軽減の両方に貢献するため、今後の発展が期待されています。