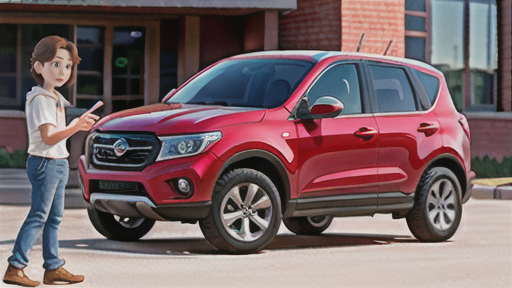
車の組み立てとブロック溶接
車は、たくさんの部品を組み合わせて作られています。まるで家を作るように、土台となる骨組みから少しずつ組み立てていくのです。その組み立て方のひとつに、ブロック溶接と呼ばれる方法があります。
ブロック溶接とは、車体全体を一度に作るのではなく、いくつかの部分に分けて溶接し、最後にそれらを組み合わせて完成させる方法です。たとえば、床の部分や側面の部分、屋根の部分など、それぞれを独立したブロックとして先に作っておきます。家の建築で例えるなら、柱や梁、壁といった部分を別々に作って、最後にそれらを組み合わせて家全体を完成させるようなものです。
なぜ、このような方法をとるのでしょうか?それは、作業の効率化と精度の向上が目的です。車体全体を一度に溶接しようとすると、溶接の熱によって金属が歪んでしまう可能性があります。また、作業スペースも広くなり、作業がしづらくなります。ブロック溶接では、小さな部品を扱うため、溶接による歪みを最小限に抑えられます。さらに、作業スペースも小さくて済むため、作業効率も向上します。
それぞれのブロックは、高い精度で溶接されます。そして、出来上がったブロック同士を組み合わせて、最終的に車体全体を完成させます。ブロック同士の溶接も、ズレや歪みが生じないように慎重に行われます。このように、ブロック溶接は、車体作りの基礎となる重要な工程であり、高品質な車を作るために欠かせない技術なのです。まるで、頑丈な家を作るために、土台や柱をしっかりと組み立てるように、ブロック溶接は車の安全性を支える重要な役割を担っています。