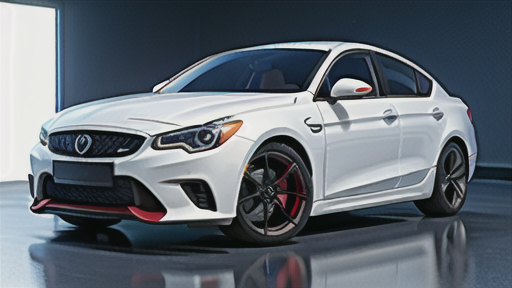
回転体の振動を抑える動釣合わせ
私たちの暮らしの中には、洗濯機や冷蔵庫、自動車など、回転するものが数多く存在します。これらが円滑に動くためには、回転する部分が「釣り合い」が取れていることがとても重要です。この釣り合いが取れていないと、振動が発生し、大きな音の原因となったり、部品のすり減りを速めたり、最悪の場合は機械の故障につながることもあります。回転体の釣り合いを調整することを「釣合わせ」と言います。釣合わせは、回転体の重さのバランスを整えることで、回転中の振動を最小限に抑えるための大切な技術です。
回転体の釣合わせには、大きく分けて二つの種類があります。静釣合わせと動釣合わせです。静釣合わせは、回転体を回転させずに重心のずれを修正する方法です。例えば、タイヤのホイールであれば、回転軸を中心に静止させた状態で、重い部分を見つけて軽い部分を付け加えることでバランスを整えます。この方法は、回転数が低いものや、回転軸方向の寸法が短いものに向いています。一方、動釣合わせは、回転体を実際に回転させて振動を測定し、修正する方法です。回転数が速いものや、回転軸方向の寸法が長いもの、例えば、自動車の駆動軸やタービンの回転軸などでは、静釣合わせだけでは不十分な場合があります。このような場合には、動釣合わせを行い、回転中の遠心力による振動も考慮してバランス調整を行います。
釣合わせは、機械の寿命を延ばし、騒音を減らし、快適な動作を実現するために欠かせない技術です。洗濯機が静かに脱水できるのも、自動車がスムーズに走れるのも、この釣合わせ技術のおかげと言えるでしょう。近年では、釣合わせの技術も進化しており、コンピューター制御による高精度な釣合わせが可能になっています。これにより、より精密な機械の製造や、より静かで快適な乗り物の開発につながっています。