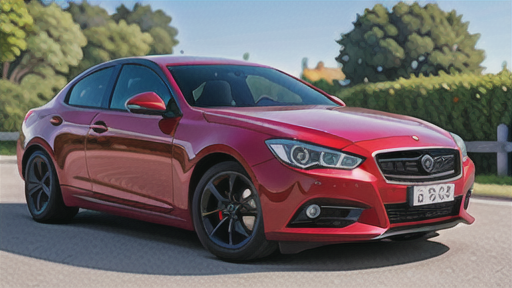
クルマを支える転造技術
転造とは、金属の加工方法の一つです。金属の棒や管に、硬い工具を押し当て回転させることで、金属を塑性変形させて目的の形を作る方法です。材料を削り取ってしまう切削加工とは大きく異なり、材料を押しつぶして変形させるため、材料の無駄がほとんどありません。このため、材料費を抑えることができ、環境にも優しい加工方法と言えます。また、転造加工は、短い時間で大量の部品を製造できるため、製造コストの削減にも大きく貢献しています。
身近な例では、ねじや歯車の製造によく使われています。ねじの場合、転造ダイスと呼ばれる工具を使い、金属の棒にねじ山を形成します。歯車も同様に、転造ホブという工具を用いて歯の形を成形します。切削加工でねじや歯車を製造すると、削り取った金属屑が発生し、材料の無駄が生じますが、転造加工では、金属を塑性変形させるだけで、材料を無駄にすることなくねじや歯車を製造できます。
自動車部品では、ボルトやシャフト、ベアリング部品など、様々な部品の製造に転造技術が活用されています。自動車の軽量化が求められる中、部品の小型化・軽量化にも転造は有効です。高強度な材料を効率的に加工できるため、より軽く、より丈夫な自動車部品の製造が可能になります。
このように転造加工は、材料の節約、製造時間の短縮、高強度部品の製造など、多くの利点を持つことから、自動車産業をはじめ様々な分野で広く利用されている重要な加工技術と言えるでしょう。近年では、より精度の高い加工や複雑な形状の成形も可能になってきており、今後の更なる技術発展にも期待が寄せられています。