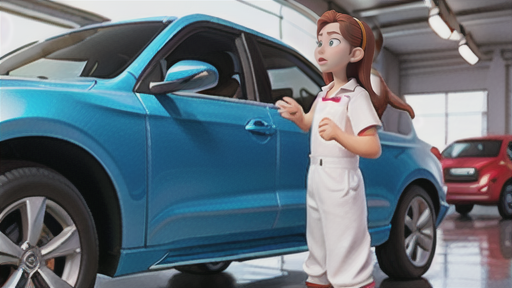
クルマづくりにおける内製とは?
車は、実に多くの部品が集まってできています。小さなネジから大きな車体まで、一つ一つの部品が車の性能や安全に深く関わっています。これらの部品をどのように作るか、どこで作るかは、車作りにおいて大変重要な決め事なのです。
大きく分けて、自社工場で部品を作る「内製」と、外の会社に部品作りを頼む「外製」の二つの方法があります。内製は、自社の工場内で部品を生産する方法です。設計図通りに部品が作られているか、品質に問題がないかを徹底的に管理できるので、高い品質の部品を安定して供給できます。また、技術やノウハウを社内に蓄積できるため、将来の車作りに役立てることができます。しかし、工場を建てるためにお金がかかったり、たくさんの人を雇う必要があったりと、費用がかさむのが難点です。
一方、外製は、部品作りを専門とする会社に依頼する方法です。内製に比べて、初期費用を抑えられることや、専門の会社ならではの高度な技術や設備を活用できるといった利点があります。部品メーカーは様々な自動車メーカーに部品を供給しているので、大量生産によるコスト削減効果も期待できます。しかし、納期や品質の管理を外部に委ねることになるので、密な情報共有や連携が不可欠です。また、自社で部品を作らないため、技術の蓄積という面では内製に劣る部分もあります。
自動車メーカーは、車の性能やコスト、そして生産の効率などを考え、部品ごとに内製と外製のどちらが良いかを判断します。例えば、車の性能に直結する重要な部品や、高度な技術が必要な部品は内製し、汎用性の高い部品や大量生産が必要な部品は外製するといった具合です。このように、自動車メーカーは様々な要素を考慮し、最適な生産方法を選択することで、高品質で安全な車作りを実現しているのです。