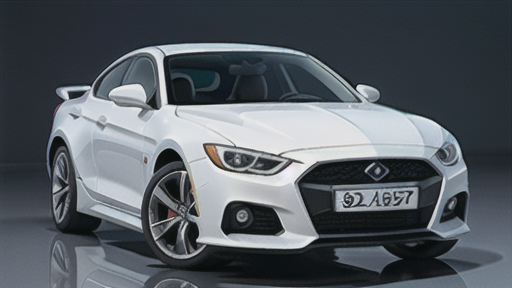
車の進化を支える無機繊維
無機繊維は、鉱物や岩石など、自然界に存在する無機物から作られたり、人工的に合成されたりする繊維の総称です。私たちの身の回りには、実に様々な種類の無機繊維が存在し、それぞれ異なる特徴を活かして、多様な用途で活躍しています。代表的なものとしては、ガラス繊維、セラミックス繊維、炭素繊維などが挙げられます。かつては石綿も主要な無機繊維として広く使われていましたが、健康への悪影響が明らかになったため、現在は使用が厳しく制限されています。
ガラス繊維は、珪砂や石灰石などを高温で溶かして繊維状に加工したものです。ガラス繊維は軽くて丈夫な上、熱や電気を通しにくいため、建物の断熱材であるグラスウールや、光信号を伝える光ファイバーケーブルなどに利用されています。また、プラスチックに混ぜ込んで強度を高める補強材としても広く使われています。
セラミックス繊維は、アルミナやジルコニアなどのセラミックスを原料とする繊維です。非常に高い耐熱性を持つことが特徴で、工業炉や窯などの高温環境で使用される断熱材や、航空宇宙分野のエンジン部品などに利用されています。
炭素繊維は、アクリル繊維などを高温で処理することで作られる、炭素を主成分とする繊維です。軽くて強いだけでなく、熱にも強いという優れた特性を持っています。そのため、航空機や自動車の車体、スポーツ用品のラケットや自転車のフレームなど、軽さと強度が求められる様々な製品に利用されています。特に、近年では自動車の軽量化による燃費向上が重要な課題となっており、炭素繊維の需要はますます高まっています。
このように、無機繊維は私たちの生活を支える様々な製品に使われており、今後も新しい種類や用途が開発されていくと考えられます。それぞれの特性を理解し、適切な無機繊維を選ぶことが重要です。