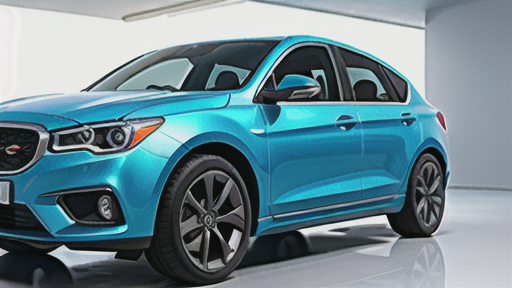
車の隠れた守護者:リン酸皮膜
車は、常に風雨や強い日差し、雪など、様々な自然環境にさらされています。これらの影響から車体を守るために、塗装の下には目に見えない重要な層が存在します。それが、リン酸皮膜です。
車体は主に金属でできており、金属は空気中の水分や酸素と反応して錆びてしまいます。錆は金属の強度を低下させ、やがては車体の寿命を縮める大きな原因となります。そこで、錆の発生を防ぎ、車体を長く守るために、リン酸皮膜が活躍するのです。
リン酸皮膜は、リン酸塩という物質を金属表面に反応させることで作られる薄い膜です。この膜は、金属表面にしっかりと密着し、まるで鎧のように金属を包み込みます。そして、錆の原因となる水分や酸素が金属に触れるのを防ぎ、錆の発生を抑制します。
さらに、リン酸皮膜にはもう一つの重要な役割があります。それは、塗装の密着性を高めることです。リン酸皮膜は、金属表面に微細な凹凸を作り、塗装との接着面積を広げます。これにより、塗装が剥がれにくくなり、車体の美観を長く保つことができます。
リン酸皮膜は、私たちには見えないところで車体を腐食から守り、塗装の密着性を高めることで、車の寿命を延ばす重要な役割を果たしています。まさに縁の下の力持ちと言えるでしょう。