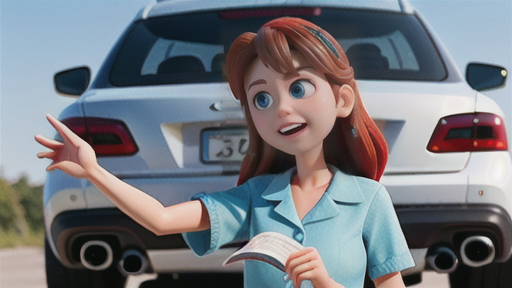
樹脂プロペラシャフト:未来の車の駆動軸
車は、心臓部である原動機が生み出した力を、路面に接する車輪に伝えることで、はじめてその役目を果たすことができます。この力の伝達の過程で、重要な役割を担う部品の一つが駆動軸です。原動機の回転運動を、車輪に伝えるための軸、それが駆動軸です。
駆動軸は、これまで長い間、鋼鉄の管で作られてきました。鋼鉄は強度が高く、回転する軸に求められる耐久性にも優れているため、当然の選択でした。しかし、近年の材料技術の進展は目覚ましく、鋼鉄に代わる新たな素材が自動車の様々な部品に用いられ始めています。駆動軸も例外ではなく、樹脂製の駆動軸が登場し、自動車業界で大きな注目を集めています。
樹脂製の駆動軸は、従来の鋼鉄製のものと比べて、いくつかの大きな利点を持っています。まず挙げられるのは軽量化です。樹脂は鋼鉄よりも比重が小さいため、同じ形状の軸を作る場合、樹脂製の方が軽くなります。車の部品を軽くすることは、燃費の向上に直結するため、大変重要な要素です。さらに、樹脂は鋼鉄よりも振動を吸収する能力に優れています。そのため、樹脂製の駆動軸を用いることで、車全体の静粛性を向上させる効果も期待できます。
鋼鉄製から樹脂製への転換は、自動車の進化における大きな一歩と言えるでしょう。かつては想像もつかなかったような技術革新が、材料技術の進歩によって実現されています。この樹脂製の駆動軸は、今後の自動車開発において、ますます重要な役割を担っていくと考えられます。今回は、このような多くの利点を持つ樹脂製の駆動軸について、その特性や製造方法、そして将来展望などを詳しく解説していきます。