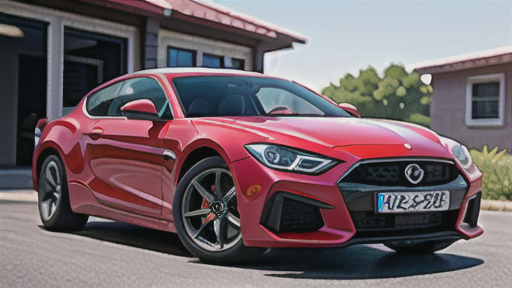
車の心臓部、ピストンの進化:スケルトン型
車は、走るためにエンジンを動力源として使っています。そのエンジンの中で、なくてはならない部品の一つにピストンがあります。ピストンは、エンジンの心臓部とも言える筒の中(シリンダー)で上下に動き、燃料が燃える力を回転する力に変える大切な役割を担っています。
ピストンには様々な種類がありますが、近年注目されているのが骨組み型(スケルトン型)ピストンです。名前の通り、骨組みのような構造で、とても軽いピストンです。従来のピストンと比べて、必要のない部分を削り落とした構造にすることで、軽さを実現しています。
この軽さが、様々な利点をもたらします。エンジンの回転が滑らかになり、燃料の消費を抑え、さらに力強さも増します。アクセルを踏んだ時の反応も良くなり、思い通りに車を走らせることができます。
骨組み型ピストンは、単に軽いだけでなく、高い強度も持っています。エンジンの内部は高温高圧な環境ですが、骨組み型ピストンはその過酷な環境にも耐えられるように設計されています。そのため、長期間に渡って安定した性能を発揮することができます。
このように、骨組み型ピストンは、燃費の向上、出力の向上、そして高い耐久性という多くの利点を持つ、まさに現代の車にとって理想的なピストンと言えるでしょう。これからの自動車開発において、骨組み型ピストンはますます重要な役割を担っていくと考えられます。