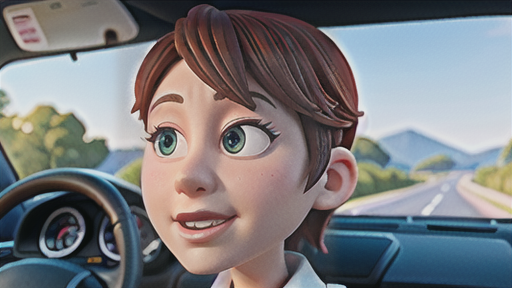
車の面取り:安全性と美しさの追求
車は、安全で美しく、快適であることが求められます。それを実現するために、車作りにおける様々な工夫の中で、表面を滑らかにする「面取り」は小さな変更ながらも重要な役割を果たします。面取りとは、部品の角を落として丸みを帯びさせる加工のことです。一見、細かな部分のように見えますが、安全性と美しさの両面に大きな影響を与えます。
まず、安全性の観点から見てみましょう。歩行者と車が衝突する事故を考えてみてください。もし、車の前面が鋭利な角で構成されていたら、歩行者は大きな怪我を負う危険があります。ボンネットの先端やバンパーの角などは、衝突時に歩行者と接触しやすい部分です。これらの場所に面取りを施すことで、角が丸みを帯び、衝撃を和らげ、歩行者の怪我の程度を軽減することができます。これは、事故の際に被害を最小限に抑える上で非常に重要な要素です。
また、乗員にとっても面取りは安全性と快適性を高めます。例えば、ドアの縁や窓枠などは、乗員が日常的に触れる部分です。これらの部分に鋭い角があると、不意に手が当たって怪我をする可能性があります。面取りすることで、角が滑らかになり、乗員が安心して車に乗り降りしたり、窓を開閉したりすることができます。さらに、車内での快適性も向上します。
美しさの面でも、面取りは効果を発揮します。面取りが施された車は、滑らかで流れるような印象を与えます。光が反射する様子も美しく、高級感や洗練された雰囲気を醸し出します。小さな面取り加工ですが、車の全体的な印象を大きく左右する重要な要素と言えるでしょう。
このように、面取りは安全性と美しさ、そして快適性を向上させるために欠かせない技術です。小さな配慮が、車を使う人々の安心と満足につながるのです。