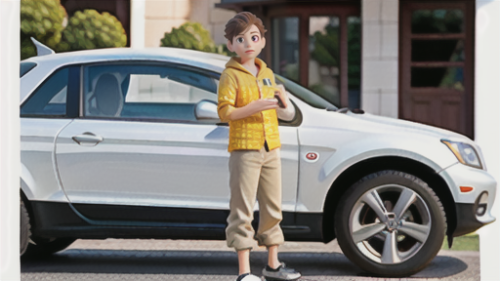
車の内装に隠された秘密:しぼ模様の奥深さ
車の内装部品をよく見ると、表面に様々な模様があることに気が付きます。この模様は「しぼ」と呼ばれ、単なる飾り以上の役割を持っています。しぼとは、金型に施された模様が樹脂部品に転写されたもので、まるで梨の皮のような細かい凹凸や、革製品のような皺模様、布のような織り目模様など、様々な種類があります。
金型に模様を付ける加工のことを「しぼ加工」と言います。この加工は、製品の見た目や手触りを大きく左右する重要な工程です。しぼ模様によって、車の高級感や活動的な印象など、受ける感じ方が大きく変わります。そのため、車の設計において、しぼ模様は重要な要素の一つとなっています。
例えば、高級車では、革のような皺模様がよく使われます。これは、しっとりと落ち着いた雰囲気を出し、上質さを演出するためです。一方、活動的な印象を与えたいスポーツカーでは、炭素繊維を模した幾何学模様が使われることもあります。この模様は、先進的で力強いイメージを車に与えます。
また、しぼには見た目以外にも機能的な役割があります。細かい凹凸をつけることで、光の反射を散乱させ、ギラツキを抑える効果があります。これにより、運転中の目の疲れを軽減することができます。さらに、小さな傷を目立ちにくくする効果もあります。例えば、樹脂部品に物が当たって擦り傷がついても、しぼ模様の中に傷が紛れて目立たなくなるのです。
このように、しぼ模様は車の個性を表現するだけでなく、快適性や実用性にも貢献しているのです。普段何気なく目にしている車の内装部品ですが、そこには様々な工夫が凝らされていると言えるでしょう。