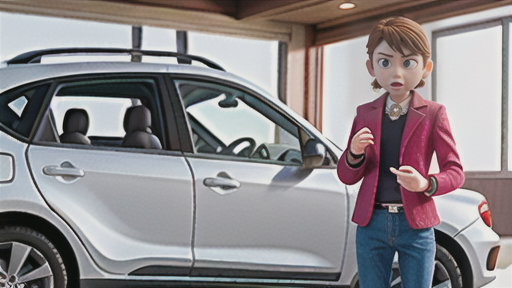
電子ビーム焼入れ:高精度な表面処理
金属の表面を硬くする熱処理方法の一つに、電子を使った焼き入れがあります。これは、電子ビーム焼入れと呼ばれています。高いエネルギーを持つ電子を材料の表面に当てることで、ごく短い時間で表面の温度を上げます。まるで太陽光を集めて物を燃やすように、電子ビームも熱源として使われます。ただし、電子ビームは太陽光よりもはるかに強力で、ピンポイントで熱を伝えられるのが特徴です。
電子ビームを当てて表面の温度が上がったら、すぐにビームを止めます。すると、熱い表面から内部へと熱が伝わり、冷やされることで表面が硬くなります。これは、熱い鉄を水で急冷して硬くする焼き入れと同じ原理です。ただし、電子ビーム焼入れの場合は、水などの冷やすものを使わず、材料自身が冷える力を使うところが違います。
この方法の優れている点は、熱を入れる場所や深さを細かく調整できることです。普通の焼き入れのように材料全体を熱するのではなく、表面の一部だけを硬くすることもできます。そのため、部品の形が複雑な場合や、特定の場所だけを硬くしたい場合に最適です。また、熱による変形も少ないため、精密な部品にも使えます。
電子ビーム焼入れを使うことで、材料の表面は硬くなり、摩耗しにくくなります。摩耗とは、物が擦れ合って表面が削れることです。例えば、歯車や軸受など、常に他の部品と接触する部分にこの技術を使うと、部品の寿命を延ばすことができます。また、繰り返し負荷がかかることで壊れるのを防ぐこともできます。これは、金属疲労と呼ばれる現象に対する強度を上げる効果によるものです。つまり、電子ビーム焼入れは、物の表面を強くし、長持ちさせるための有効な方法と言えるでしょう。