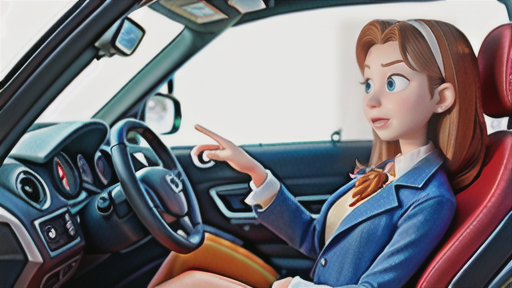
電気炉:未来を照らす金属溶解の炉
金属を溶かすための熱源に電気を用いる装置、電気炉。大きく分けて三つの種類があります。一つ目は、電磁誘導を利用して金属自身を発熱させる誘導炉です。磁気を帯びた金属に電気を流すと熱が発生する性質を利用しています。誘導炉の中には、高周波と低周波の二種類があります。高周波誘導炉は、比較的小さな金属を溶かすのに適しており、精密な温度調節が可能です。一方、低周波誘導炉は、大きな金属を溶かすことができますが、温度調節は高周波誘導炉ほど精密ではありません。溶かす金属の種類や量、求められる品質によって、高周波と低周波を使い分けます。二つ目は、電極と金属の間に起こる放電現象を利用したアーク炉です。電極と金属の間に高い電圧をかけると、激しい火花が発生し、その熱で金属を溶かします。アーク炉は、一度に大量の金属を溶かすことができるため、主に鉄鋼の製造などに使われています。しかし、温度調節が難しく、溶けた金属の品質が均一になりにくいという欠点もあります。三つ目は、電熱線に電気を流して発熱させる抵抗炉です。電熱線は、電気を流すと熱くなる性質を持つ金属線です。抵抗炉は、温度調節が容易で、比較的小規模な溶解に適しています。また、他の二つの炉に比べて構造が単純で、扱いやすいという利点もあります。このように、電気炉にはそれぞれ異なる特徴があります。溶かす金属の種類や量、求められる品質、設備の規模などを考慮し、最適な電気炉を選択することが重要です。