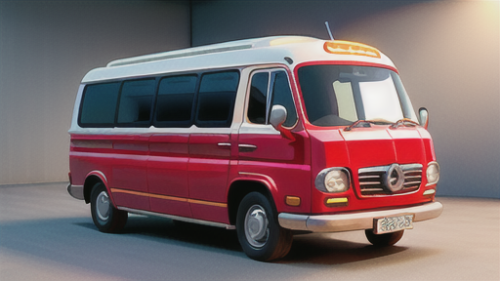
バンボディ:トラック荷台の基礎知識
荷物を運ぶための働く車、トラック。その荷台部分には、箱型の荷室であるバンボディが取り付けられています。このバンボディこそが、様々な荷物を安全に目的地まで届けるための重要な役割を担っています。一口にバンボディと言っても、実はその種類は様々です。
まず、皆さんがよく目にするのは、乾いた荷物を運ぶためのドライバンでしょう。これは、日用品や衣類、家具など、雨風にさらされても問題ない荷物を運ぶのに適しています。荷物の積み下ろしがしやすいように、後部扉だけでなく側面にも扉が設けられているものもあります。
次に、温度管理が必要な荷物を運ぶための保冷バンがあります。生鮮食品や冷凍食品など、温度変化に弱い荷物を運ぶ際に活躍します。このバンボディは、断熱材で囲まれた構造になっており、冷蔵ユニットを搭載することで庫内温度を一定に保つことができます。
また、荷物の積み下ろしを効率的に行うために、パワーゲートやテールリフトといった装置が備え付けられているバンボディもあります。パワーゲートは、荷台後部に設置された昇降機で、荷物を地面から荷台までスムーズに持ち上げることができます。テールリフトは、荷台後部に取り付けられた折りたたみ式の板状の装置で、荷物を台車ごと荷台に載せることができます。これらの装置は、作業負担を軽減するだけでなく、積み下ろし時間の短縮にも貢献します。
さらに、バンボディの材質も重要な要素です。従来は鉄製が主流でしたが、近年では軽量化のためにアルミや樹脂製のバンボディも増えてきています。軽量化は、燃費向上や環境負荷低減につながるだけでなく、積載量の増加にも貢献します。
このように、バンボディには様々な種類があり、運ぶ荷物や用途に合わせて最適なものを選ぶことが大切です。荷物を安全に確実に運ぶためには、バンボディの特性を理解し、適切な選択をすることが不可欠です。