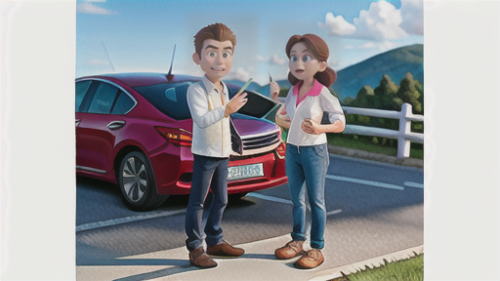
駆動を支える十字軸:その重要性
自動車の心臓部である原動機で生み出された回転力は、最終的に車輪に伝わることで、初めて車は前に進みます。この回転力を伝えるために、重要な役割を果たす部品の一つが十字軸です。十字軸は、回転する二本の軸の間の角度が変わっても、滑らかに回転運動を伝え続けるという、特殊な働きをします。
原動機の力は、まず変速機を通じて駆動軸に送られます。この駆動軸と、車輪につながる後輪軸との間には、十字軸が組み込まれています。道路の凸凹や段差を乗り越える際に、車体は上下に揺れます。この揺れに連動して、駆動軸と後輪軸の角度も常に変化します。もし、この二つの軸を硬く繋いでしまうと、角度の変化に耐えられず、部品が破損したり、回転がスムーズに伝わらなくなったりするでしょう。
このような問題を解決するのが十字軸です。十字軸は、二つの軸が交わる角度が変化しても、滑らかに回転運動を伝えられるように工夫されています。十字型に組まれた部品が、軸の角度変化を吸収し、途切れることなく回転力を伝達するのです。
十字軸は、別名カルダン式、あるいはフック式自在継ぎ手とも呼ばれます。その構造は、二つの軸のそれぞれにヨークと呼ばれるU字型の部品が取り付けられ、この二つのヨークを十字型をした部品で連結することで構成されています。この十字型の部品が、軸の角度変化を吸収する要です。
もし十字軸がなければ、原動機の回転力は車輪にうまく伝わらず、車はスムーズに走ることができません。十字軸は、普段は目に触れることはありませんが、自動車の動きを支える重要な部品なのです。まさに、縁の下の力持ちと言えるでしょう。