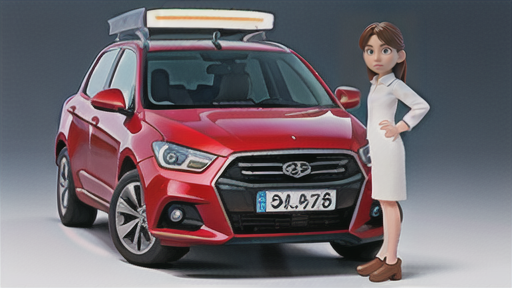
車の内装部品を形づくる熱成形
熱成形は、熱を利用してプラスチック材料を成形する技術です。私たちの身の回りにある自動車には、様々な部品が使われていますが、実はその多くにこの熱成形技術が用いられています。
まず、熱成形ではプラスチックの板を加熱炉などを使って高温で温め、柔らかくします。この時、プラスチックの種類によって適切な温度が異なり、材料の特性に合わせて精密に温度管理を行う必要があります。十分に柔らかくなったプラスチック板は、金型にセットされます。
次に、柔らかくしたプラスチック板を金型に押し当て、目的の形に成形します。この工程では、真空成形や圧空成形といった様々な方法が用いられます。真空成形は、金型とプラスチック板の間に真空状態を作り出し、大気圧によってプラスチックを金型に密着させる方法です。一方、圧空成形は、圧縮空気を用いてプラスチックを金型に押し付ける方法です。
成形されたプラスチックは、金型の中で冷却され、最終的な形状が固定されます。冷却方法も様々で、空冷や水冷など、成形する部品の形状や材料に合わせて最適な方法が選ばれます。このようにして、複雑な形状の部品でも一体成形で作り出すことが可能になります。
熱成形には多くの利点があります。複雑な形を一体で成形できるため、部品同士の接合が不要になり、製造工程を簡略化できるだけでなく、組み立てにかかる手間や時間を削減し、製造費用を抑えることにも繋がります。また、金属材料に比べてプラスチックは軽量であるため、部品を熱成形で製造することで自動車全体の軽量化に貢献し、燃費の向上も期待できます。
このように、熱成形は自動車産業において重要な役割を担っており、自動車の進化を支える技術の一つと言えるでしょう。